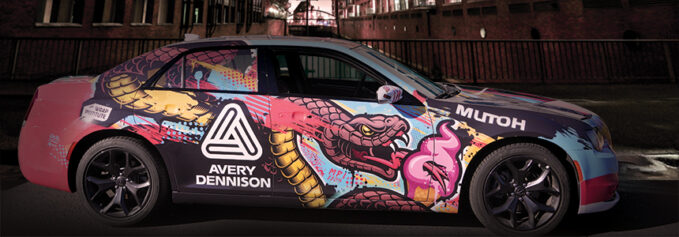
By Cassandra Balentine
Vehicle wraps are subject to many potentially damaging elements day in and day out. Therefore, vehicle graphics—partial or full—benefit from an overlaminate to ensure success throughout the intended lifecycle.
Above: Avery Dennison DOL 1360 Max is a 1.3-mil film that offers extended durability.
Continued Advancements
Along with ink and media, overlaminates continue to advance to ensure flexibility, durability, and sustainability.
In recent years, vehicle wrap overlaminates have undergone advancements, specifically targeting durability, visual appeal, and user friendliness. “These improvements aim to satisfy the demands of both professional installers and vehicle owners seeking top-notch finishes for their vehicles,” offers Daniele Perotti, global graphics product and business development manager, Fedrigoni Self-Adhesives (FSA) North America.
Material finish has also changed. “Improvements in casting the sheets used to manufacture the film have made significant improvements in terms of finish. The gloss clarity and vibrancy are higher, and the matte finish is more refined and consistent,” shares Amanda Smith, marketing communications, graphic and signage solutions, Mactac.
That said, as critical as laminate protection is to the wrap industry and the work that installers conduct, Sam Crosby, dealer manager, Graphic Finishing Partners, LLC, feels that the majority of laminates have stayed relatively the same. “While cast gloss still dominates the products sold, having luster, satin, and matte options is always a possibility and typically dictated by the consumer. There have been advancements relating to thinner, more eco-friendly products, but price and availability still influence what the consumer ultimately chooses to use.”
Advancements in overlaminates for vehicle graphics target specific functions like flexibility, conformity, and durability.
Perotti says flexibility developments are designed to improve the ease of application of overlaminates. “These include advanced adhesive technologies that make application easier and allow for repositioning during installation.”
Molly Waters, senior technical specialist, Avery Dennison Graphics Solutions, points out that polyurethane films that are now available help provide extra conformability and flexibility for use on three-dimensional surfaces.
Laminates boast greater flexibility, allowing them to conform readily to the curves and contours of vehicles. “This flexibility is crucial for achieving seamless finishes without wrinkles or creases, especially around challenging areas like bumpers, mirrors, and curves,” shares Perotti.
Durability is a primary requirement. “It is a key feature of vehicle graphics. Enduring the elements, road conditions, and typical wear and tear on vehicles is immensely valuable,” says Perotti.
“Durability continues to be a focus, as we know it is important for print and sign shops and brand owners to have protected, high-quality graphics for extended periods of time in a variety of climates,” adds Alex Fox, product manager, Avery Dennison Graphics Solutions.
Specific to wrap laminates, Crosby says durability ranges from five to ten years, depending on how each manufacturer decides to offer that protection, durability, and manufacturer warranty.
Base Considerations
Overlaminates are generally developed in tandem with base material counterparts.
“Developing the overlaminate together with the print media is extremely important,” offers Perotti. The performance of the overlaminate must match or support the performance requirements the print film provides. This makes for a fully compatible product that meets the needs of the industry.”
Ensuring that the overlaminate aligns with the performance criteria of the print film is crucial. For example, if you had a very flexible, conformable print media and married it with a rigid laminate, it would affect the overall performance of the material. “The flexibility of the print media would be negatively impacted by the rigidity of the overlaminate. The lamination film needs to match the print media flexibility in order to have a uniform behavior for the material,” stresses Perotti.
Waters says Avery Dennison always considers the durability of the complete construction or application as it develops films and overlaminates. “It is important to match the appropriate overlaminate and base material. For example, it is never recommended to apply a calendered laminate to a cast base material. Applying a lesser performing film to a higher performing film will reduce the overall performance properties of the base film.”
“Manufacturers warrant the combination of the overlaminate and media together because they understand both characteristics and can recommend the best combination. It also allows for consistent quality control throughout the manufacturing process, which gives better results during the application,” adds Smith.
Crosby admits that advancements in media are still where most manufacturers decide to invest in innovation. “Laminate thicknesses, release liners, base polymers, and finishes have remained relatively unchanged over the past few years. But manufacturers will create overlaminates to work best for customer expectations.”
He estimates that the largest wrap shops choose to keep the media/laminate combination with the manufacturer of choice, often dictated by the installer or shop that is creating the work. Others will mix/match based on availability and price. “Warranty and piece of mind are often the driving forces for some larger, more established shops but the market is changing and shops and installers will often use one brand of print media while using a different manufacturer’s overlaminate,” continues Crosby.
Full and Partial
Certain overlaminates are designed to work better for full or partial wraps.
For example, “FSA’s Ri-Jet C50 Ultimate Slide & Tack product is specifically engineered for full vehicle wraps. In cases where a more economical option is preferred, installers often recommend a partial vehicle wrap,” shares Perotti.
FSA does offer an alternative choice when high conformability isn’t essential, particularly for partial wraps. The Ri-Jet P75 SB Airflow, a polymeric vinyl-coated material with a solvent-based adhesive featuring air egress channels, is an ideal film specifically tailored for partial wraps.
For full wraps, Waters feels that the best performance is typically going to be with cast or polyurethane laminates. “These laminates offer the best conformability to the contours of a vehicle. For partial wraps, if there are only simple curves to consider, then you could get by using a print media and even a calendered laminate; however, it is important to note that the durability could be reduced due to the lower durability on calendered films.”
“For full wraps, thinner, more flexible overlaminates are preferred, as they can better conform to the curves and contours of the vehicle. Thicker and more durable overlaminates are recommended for partial wraps, as they provide added protection against abrasion. Ultimately, the choice of which overlaminate to use will depend on the project’s specific requirements, including durability and longevity,” shares Smith.
Crosby feels that choosing the best overlaminate for a partial versus full wrap really depends on where the graphic is installed. This is particularly true for partial wraps. “If the wrap is intended to cover recessed areas, rivets, and bumpers or oddly shaped surfaces, essentially being stretched to conform to areas that are not considered flat, cast laminates are always the right choice. The ability to stretch and conform is only achievable with the most conformable media and laminate. Calendared films potentially will fall short of meeting those requirements.”
A great general rule is to always use equal or better grades of laminate to the grade/quality of the print media, shares Crosby. “An example would be using a cast overlaminate to protect a polymeric calendared media.”
Skipping the Overlaminate
For printed vehicle graphics, overlaminates are overwhelmingly recommended by the experts.
For very short-term wraps—generally less than 12 months—Crosby says you could technically avoid using an overlaminate. “But this would leave the image susceptible to damage from road debris, chemicals if washed, and makes for a more cumbersome installation process. One of the key benefits of laminating vehicle graphics is how it assists in applying the graphic, adding slight rigidity to the printed vinyl and making the graphic easier to install.”
“If the vehicle wrap will only be used for a short period, it’s possible to use a non-laminated film. However, this isn’t recommended as the printed surface might be susceptible to scratches or damage. Furthermore, lacking an overlaminate could result in the film having insufficient rigidity, especially when used in large formats,” comments Perotti.
Waters stresses that vehicle wraps always need some sort of protection over the printed graphic. “The laminate is going to protect the ink from abrasion, UV from the sun, chemicals, etc.”
However, when referencing non-printed wraps, such as a color change job, overlaminates are not required.
Perotti says FSA actually advises against using an overlaminate on colored vinyl. “Transparent films might deteriorate faster than colored ones, potentially causing a yellowish tint to develop on the colored vinyl over time.”
Waters also doesn’t recommend applying overlaminates to color change films, as they are designed to be used right off of the roll. “They have the overlaminate built into the construction.”
Considering Overlaminate
It is highly suggested that printed vehicle graphics utilize a quality overlaminate to ensure success for the intended lifecycle. These graphics regularly face harsh elements and media vendors offer durability without compromising flexibility.
Mar2024, Digital Output