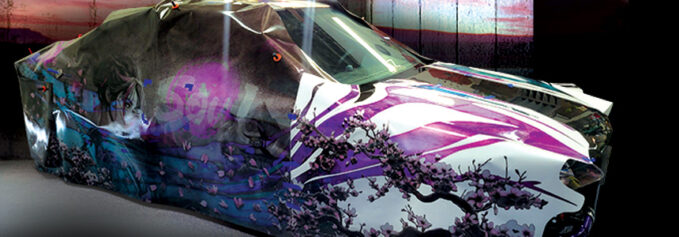
By Melissa Donovan
Vehicle wrap installers—professional, amateur, hobbyist, and everything in between—turn to the newest films and media to create efficiencies in the application process, as well as enhance the overall look of the final product.
A combination of the proper adhesive, liner, and material helps achieve a successful vehicle wrap application. Today’s newest options boast updates to release liners, repositionability, bubble-free installation, and bonding strength.
“These innovations not only enhance the installation process but also deliver a smoother, more professional finish, allowing installers to focus on precision and efficiency,” attests Ryan Allen, regional technical specialist, Avery Dennison Graphics Solutions.
Here, we take a look at each component—release liners, repositionability, bubble-free installation, and bonding strength—and recent improvements.
Above: Shop Vinyl Vixen Wraps of AZ printed this latest design on a Mutoh America, Inc. printer. The shop sets the printed graphic panels of this Japanese-motif full car wrap in sections where it will be applied on a Honda Civic. This is a recommended first step before installing a full wrap, especially one with a complicated design. The wrap features Avery Dennison Supreme Wrapping Film in Matte Metallic Silver, Avery Dennison Chrome in Gloss Silver, and DOL 1360Z protective overlaminate.
Catch and Release
Advancements in release liner technology continue to propel vehicle wraps forward.
Marco Boyer, co-founder, Omega-Skinz, which is produced in conjunction with Grafityp and SOTT International, explains that the first release liners were mostly made up of siliconized paper and were much thinner than today’s iterations. This led to curling and disintegration when they came in contact with moisture. “Today’s better liners are sealed with a layer so this can no longer happen. Also, the air channels are shallower and have a different structure.”
Improvements to release liners influence both the installation process and the final appearance of vehicle wraps, says Trip Harris, business development manager, General Formulations. “Advanced release liners now allow for adjustable degrees of release, reducing static and speeding up liner removal during installation. Additionally, air egress patterns are less visible on the surface, which sharpens the depth of color and enhances the overall visual appeal of the wrap.”
“Release liner advancements include the pattern of the structure as well as the release characteristics of the liner from the adhesive. The liner structure creates air channels in the adhesive. The pattern in the adhesive allows the liner’s slideability on the vehicle’s surface and the release of the air behind the film. This helps with the positioning of the graphic and the ease of application. The release of the liner has to be good enough not to tunnel when printing but easy enough to expose the adhesive when ready to install. Both of these advancements allow for easier and faster installation, which is key to profitability,” admits Nate Goodman, product manager, Mactac.
Allen agrees that significant enhancements have occurred in recent years, like liners being carefully formulated to ensure a smooth release and excellent lay flat properties.
“Recent advancements in structured release liners have significantly simplified the car wrapping process. These innovations ensure smooth application and enhance product performance. Enhancement improves the overall aesthetic of the installed wrap, elevating the finished product’s appearance,” explains Daniele Perotti, PM and BPM graphics and industrial, Fedrigoni Self-Adhesives.
Repeated Moves
Another critical component to vehicle wrap media is its ability to be repositioned repeatedly during the installation process.
“Historically, excessive repositioning could lead to air channel collapse, causing imperfections in the final application. However, newer liner and film combinations are designed to withstand multiple adjustments without sacrificing performance,” shares Harris.
Repositionability and adhesive technology go hand in hand. Developments in pressure-sensitive adhesives allow for low initial tack, this enables the film to be repositioned without affecting adhesion capability, notes Allen. This is “critical in providing installers with the flexibility to align graphics accurately and make adjustments without stretching or distorting the material, leading to a flawless final wrap.”
Low tack is only one part of the repositionability equation. Making the process more straightforward is the combination of a low-tack adhesive with a micro-structured liner, according to Perotti. “This reduces the adhesive contact area on the vehicle’s surface, allowing easy repositioning. Over time, the adhesive flows through the micro channels, ensuring 100 percent surface contact for secure, long-term adhesion.”
Goodman argues that repositionability can be referred to as slideability. “Slideability allows the material to be placed and moved to the correct position without the adhesive tacking to the surface of the vehicle. This provides a more accurate placement of the graphics. Once they are in place, pressure can be applied and the adhesive will bond to the surface.”
Boyer notes that while repositionability is a nice-to-have feature, a good vehicle wrap installer can successfully apply any film without it. He admits that a repositionable film does allow faster—and easier—installation.
No Bubbles, Please
The technology behind bubble-free installation continues to change for the better.
Part of the reason for this is improvements in the construction of air egress channels. “While structured liners with bubble-free technology have existed for a decade, earlier versions often resulted in a grid effect as the face film collapsed into the adhesive channels,” explains Perotti.
“Advancements in air egress patterns have revolutionized bubble-free installation, not only making it easier to achieve a flawless finish but also significantly speeding up the application process. The ability to quickly eliminate air bubbles is the result of improvements in both film and liner technology. Additionally, enhanced cleaning and installation techniques have contributed to egressing the air out of the film more efficiently,” notes Harris.
Quick transfer of airflow is key. “The amount of airflow to remove the bubbles from behind the film has increased due to the designed structure in the liner that transfers the pattern into the adhesive. The repositioning of the adhesive also allows the adhesive to be pulled up so the air can be removed as it is reinstalled,” suggests Goodman.
“Air egress channels allow air to escape during application, drastically reducing installation time and eliminating the need to puncture or work out air pockets manually. Bubble-free technology ensures that the final product looks professional and lasts longer, as trapped air can compromise the bond between the film layer, adhesive, and applied surface over time,” says Allen.
Hold Strong
A vehicle wrap needs to remain in place for its intended lifespan. This is made possible thanks to the bonding strength found in the same adhesive chemistry that allows for repositionability.
Recent improvements in adhesive chemistry enhance bonding strength, according to Allen, which helps wraps maintain their integrity over time even on complex curves, rivets, and contours.
It’s a dance between repositionability and long-term bond, as the adhesive developed for the application must perform a certain way during and after the installation.
“The adhesive needs a light initial tack to work with the pattern imparted by the liner and slide over the vehicle’s surface without sticking until pressure is applied to lock it down. It will also need to be released from the surface when pulled up to be reinstalled where needed. The adhesion must also lock down with heat and build over 24 hours to prevent lifting around complex curves or rivets,” says Goodman.
Materials need to achieve the correct balance of initial repositionability and ultimate adhesion for a strong bond when the film is set in its final position. “This is critical for long-term vehicle wraps, especially in extreme weather conditions where consistent adhesion prevents lifting or peeling,” comments Allen.
“In the past, vehicle wrapping was a labor-intensive process due to adhesives with high initial adhesion, requiring expertise and significant time to apply. Modern advancements have struck the perfect balance between low initial adhesion for easy installation and high final adhesion for long-term durability. This improvement ensures a secure bond between the film and the vehicle surface while simplifying the installation process for professionals,” states Perotti.
The same adhesive that offers repositionability and a strong bond, also must remove cleanly. “Bonding strength technology has advanced significantly, improving the ability to remove films cleanly without leaving behind adhesive residue. This has long been a challenge as improper practices often result in excessive adhesive being left on surfaces. To address this, modern adhesive systems are designed to balance a strong bond with clean removability,” shares Harris.
“Additives in adhesives often improve adhesion. But bond strength isn’t that different. Now film can be removed more easily without leaving adhesive behind,” adds Boyer.
Solving the Complexities
Release liners, repositionability, bubble-free installation, and bonding strength collaborate to achieve the ideal vehicle wrap material.
And what is the ideal material? One that lays flat over complex curves and rivets, allows for repositionability multiple times if necessary, bonds well to the surface once install is completed, and finally, removes cleanly.
It’s a complex combination of elements that scientists behind the scenes work to achieve while keeping up with other advancements in tandem, whether it is ink related or environmental.
Visit digitaloutput.net in March when an exclusive webinar on this same topic is available to view.
Mar2025, Digital Output