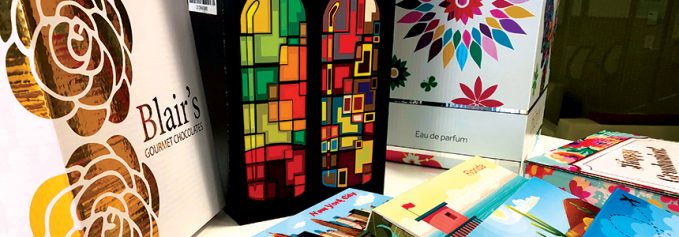
By Cassandra Balentine
Flatbed printers output to a variety of media options—including corrugate. While this substrate is notorious for its porous nature and tendency to warp, advances in media handling are incorporated into flatbed machines to reduce these issues when printing directly to board. Another option involves digital printing to rolls that are then transferred to corrugate boards. Print service providers (PSPs) looking to offer corrugate should understand the nuances of the media and determine which device is best suited to its production.
Above: The canon Oce Arizona 6100 High Flow Vacuum series of printers focuses on maximizing productivity with features that allow for easy handling of warped corrugate boards.
Packaging Trends
The use of digital printing for packaging applications is growing. Flatbed printers are commonly used to produce packaging prototypes and short runs. However, the demand for digitally printed corrugate for packaging and displays is increasing, driven by overall industry trends towards personalization, faster turnaround times, and versioning.
Becky McConnell, product marketing manager, Fujifilm North America Corporation, Graphics Systems Division, says the nature of a flatbed printer allows for repeated registration and that opens the door to a number of high-profit applications within and beyond corrugate printing, like easy two-sided printing. It also provides the fastest possible turnaround and ability to print just in time, which enables the production of on demand, short-run work and endless customizing of print campaigns. “From a cost savings standpoint, the ability to print on a digital flatbed printer eliminates prepress costs, as no plates or precoating processes are required and waste is reduced in the supply chain.”
Brands want to differentiate themselves through packaging to stand out on the shelf and engage with customers through customized, high-quality print including retail-ready stands that capture shoppers’ attention in high-profile locations in stores. Nina Starr, product marketing manager, HP Scitex HDR Industrial Presses, HP Inc., believes this specific trend continues to drive demand for corrugate digital printing.
Patrick Donigain, senior marketing specialist, Canon Solutions America, sees a demand for very short-run production, rapid prototyping, and small batch production. “Increases in very short-run package production—which are runs less than 12,000 square feet in size—are driven by regionalization of packaging, synchronization with marketing campaigns, personalization of products, and the expanding micro-brand market such as craft breweries and distilleries.”
Even though short-run digital production is growing, it still only accounts for a small percentage of overall volumes. Donigain says this opportunity leaves box and display manufacturers wondering when it makes financial sense to jump into the short-run digital market.
Supporting Corrugate Trends
The packaging industry incorporates many segments. One is corrugate, which is popular for both point of purchase (POP) display and packaging applications. Many digital flatbed printer manufacturers support corrugate packaging trends, addressing media handling challenges and incorporating value-added features attractive to this market.
Dave Cich, president, Vanguard Digital Printing Systems, cites two parallel paths of growth for corrugate. The first is high-speed, digital single-pass machines for high-volume customization of boxes, which he says is starting to create inroads into the traditional analog print portion of the box market. “The opportunity for custom marketing on boxes is in its infancy and will expand as the technology becomes more robust and dependable. Improved aqueous inks, as well as six- and seven-color solutions with UV inks are providing the colors that customers require.”
The second path involves custom short runs of one to 500 pieces. There are machines with proper vacuum hold down for corrugate box materials. “The enhanced vacuum tables on these fixed table flatbeds hold material flat, no matter how much of a curl it may have. Belt solutions do not have enough vacuum to accomplish the hold down needed,” he explains.
Cich adds that the ability to create custom boxes inexpensively for a one-to-one marketing solution is the future of packaging. “No longer will people be limited to plain white or brown boxes. Marketing will control the look moving forward.”
In today’s competitive market, corrugate box and display manufacturers know they need move into short-run digital production. “To date, their dilemma has been to justify spending millions of dollars for a digital press, which is designed to handle corrugate boards or incur tradeoffs in functionality and productivity with a general purpose digital printer,” explains Donigain.
Larry D’Amico, director of sales, large format, Durst Image Technology US LLC, points out both aqueous and UV inks support the variety of applications available to the corrugate segment, especially with the need for aqueous for any food-related application. Durst offers both aqueous and UV ink solutions
Embellishments are trending in the corrugate market based on customer requests, says Mike Kyritsi, president, swissQprint. Ways to add special effects that would otherwise require a secondary piece of equipment are important.
Jay Roberts, product manager, UV printers, Roland DGA Corporation, agrees, citing many wide format printers using UV-curing inks and lamps that offer spot white and spot gloss/varnish models. “With these additional spot colors, the packaging market has embraced UV printing technology.”
Challenge Accepted
Media handling is by far the biggest challenge PSPs face when learning to print to corrugate with a digital flatbed printer. Equipment manufacturers understand the struggle and have addressed the issue. Bulb heat and ink cracking issues are also concerns addressed by OEMs.
Bill Brouhle, senior application specialist, Agfa Graphics, admits that printing on corrugate paper products can be tricky, especially in the Winter when there is little humidity in the air.
When digitally printing to corrugate, it is essential to keep the substrate flat. The flutes found in corrugate boards create a challenge for holding down the substrate for printing.
Donigain says the key to hold down is a high flow rate, which contacts the corrugate board at a much higher percentage of the surface area. “Unless more expensive, premium boards are used, corrugate boxes will have severe warping,” warns Donigain. “In order to flatten these boards without the use of time and profit-consuming tape, the flatbeds need to overcome extremely porous liners and flutes.” He explains that standard pumps are not capable of successfully holding down corrugate boards.
Roberts notes that the edges of corrugate media are easily dinged and bent. “Digitally printing the uneven substrates can create challenges for the inexperienced operator, which must be met by understanding how the flatbed table can utilize the optimal suction of the vacuum,” he shares. Operators must also know when to restrict airflow channels to hold down the corrugate board.
McConnell admits media handling is an issue, but automated handling solutions built specifically for handling corrugate boards alleviate many of the challenges that come along with printing warped boards. She explains that flexibility within that handling system to adjust where the vacuum is generated can be additionally beneficial if there is variance to the flutes or grades of boards being printed.
Kyritsi suggests some issues result from a poor imaging surface. “Material should be selected based on cost effectiveness as well as compatibility with the ink technology being implemented.”
Print quality is another consideration. It can be difficult to simultaneously create smooth gradations, detailed highlights, and uniform solids on corrugate. “Producing smooth gradations and detailed highlights requires small picoliter drop sizes, while uniform solids require larger picoliter drops. Maximizing print quality requires the ability to produce many different drop sizes, from very small drops to very large drops simultaneously within the same print. Having these capabilities allows for the production of sharp detail, smooth gradations, and uniform solids,” shares Donigain.
D’Amico points out that like any market, certain nuances must be understood to succeed. “As an example, the engineering associated with the construction of a box can require years of training and experience. Do not underestimate the importance of these associated requirements if you are serious about entering this market,” he cautions.
Considering Features
There are many considerations when investing in a new digital flatbed printer. For those looking to print to corrugate, specific features should enter into the decision-making process. These include the right vacuum system, curing technology, and ink.
The most important feature is the ability of the machine to reliably hold material down during printing. “A consistent media surface is needed for accurate droplet placement. With that in mind, the time it takes to set up a machine is important to the productivity of the equipment. Rolls of tape cost a lot of money over the course of the year and reducing or eliminating this step can save thousands of dollars annually,” recommends Kyritsi.
A strong vacuum system is essential. “PSPs want to test their boards to ensure the system can handle what they’re producing on today, or be willing to consider a different stock if the particular printing system being considered cannot handle it,” suggests McConnell. The ability for the operator to adjust the vacuum is also a critical feature. “Just like in any other application, adjusting print quality and speed depending on a client is a consideration that many PSPs overlook with their eye on productivity.”
D’Amico urges PSPs to look for and test the ability to consistently and repeatedly run corrugate material. “You need to verify that the printer can handle the typical curled sheets and not the perfectly flat material used in many demonstration studios,” says D’Amico.
Roberts suggests purchasing a printer that includes feature-filled and user-friendly software. “Additionally, it’s important to purchase a printer from a customer-focused manufacturer who will be a partner committed to your ongoing success.”
Flatbed Offerings
To support printing to corrugate board, many flatbed printer manufacturers offer attractive features to address the common challenges and demands addressed in this article.
Agfa manufactures a variety of machines meant to directly address the needs of the direct to corrugate printing market. Of which, the top three are the Jeti Tauro H3300 LED, Jeti Tauro H2500 LED, and the Jeti Mira MG 2732 HS LED. These printers all incorporate technologies that assist PSPs attempting to differentiate themselves from the competition while maintaining extreme quality and productivity, shares Brouhle.
Canon’s Océ Arizona product line is used in the corrugate market for short-run production, sample production, and prototyping. Donigain says the company learned from years of experience within the corrugate market and incorporated specific capabilities into the Océ Arizona 6100 High Flow Vacuum series of printers. “These printers focus on maximizing productivity with features that allow for easy handling of warped corrugate boards. This improved material handling, in addition to the high print quality and low ink use of the Océ Arizona family of printers combines to produce an efficient, entry-level production printer for the corrugate market.”
CET Color offers the DG1560 direct to corrugate printer. Featuring a 61.4-inch print width, the device utilizes Kyocera printhead technology with 2,656 nozzles per printhead. It is rated at speeds of up to 492 feet per minute and can print on material up to 0.43 inches thick. The company also operates the Corrugated Single Pass 1604. Production speed reaches up to 150 meters per minute at up to 1.56 meters printing width. It is equipped with a fully automatic substrate conveying system, lead edge feeding, and powerful vacuum suction that allows stable printing with high precision.
D’Amico says Durst’s portfolio for this segment is broad, offering single- and multi-pass printing platforms. The company has solutions available that handle applications from 50 to 5,000 boards in an hour at a variety of price points. It also offers both aqueous and UV ink solutions.
EFI offers industrial, single-pass technology for corrugate printing with the Nozomi C18000. Featuring LED technology, it is designed to present a cost-effective production process to respond to customer demands for even faster job turns, versioning and variable data, and just-in-time and on demand printing while reducing inventory costs and waste.
Fujifilm’s Onset X series features a dual robotic handling system for corrugate boards. McConnell explains that the robot effector is designed specifically for handling porous, warped corrugate boards and the suction cups can be adjusted for each job.
The HP Scitex 17000 Corrugated Press delivers high productivity and vibrant image quality. It deploys automation and prints up to 1,000 square meters per hour for up to two million square meters per year. The multi-pass press allows boards to be fed two- or four-up simultaneously on a job.
Additionally, HP Scitex Corrugated Grip is an advanced media handling system that overcomes the challenges of printing on warped corrugate boards, keeping media flat for high-quality, productive printing. “It easily handles boards with a warp of up to 40 millimeters, automatically flattening and holding it down throughout the printing process. The loading table is covered by suction mat segments, positioned to ensure effective hold down of boards with varied dimensions,” shares Starr.
Roland’s VersaUV LEJ-640 UV LED wide format hybrid inkjet printer incorporates advanced VersaUV technology. Roberts says the 64-inch machine prints CMYK plus white and clear coat to virtually any substrate, from roll media to half-inch thick board stocks for premium custom graphics with special effects and finishes.
The turbine system in the swissQprint line of flatbed printers is adjustable from the amount of pressure used to the specific size range of vacuum for a given material size. “If the sheet size is smaller, the swissQprint gives you the ability to step-and-repeat multiple sheets on the table and also offers the ability to run tandem—increasing the productivity of the device,” explains Kyritsi. If a carriage collision does happen, the swissQprint offers a print-from-pass feature, which resumes a print after a collision.
Vanguard provides single pass as well as fixed table flatbed printers. The company built two different solutions for the corrugate market, the first is for high-volume customers—the VSP1400 digital screen press single-pass machine. The four-color printer prints at three linear feet per second at 720 dpi. It prints 38,000 linear feet of material in an eight hour shift and is fully automated.
For short runs, the company offers the VK300D-SS. The 5×10-foot seven-color fixed table flatbed printer features a tabletop, which is supported by two 7.5 horsepower vacuum motors. Spread over two zones, the machine continuously prints any full sheet or precut boxes. The press features Kyocera printheads that fire at 3.5 picoliters and has a print swatch of over 8.5 inches per pass. It produces custom boxes and does this at up to 1,800 dpi at speeds of up to 1,500 square feet per hour—all day and night, according to Cich.
Calling All Corrugate
Corrugate substrates opens new business opportunities for PSPs willing to take on the challenge of printing to this difficult media. Making the move is getting easier as digital flatbed printer manufacturers implement advancements like improved media handling and vacuum systems, advanced ink sets, and LED curing.
May2019, Digital Output