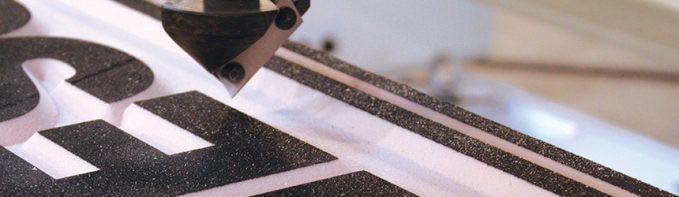
By Elizabeth Quirk
CNC routers are defined as computer-controlled cutting machines and are instrumental in any print shop looking to offer its customers repeatability when it comes to complex shape cutting. CNC routers also offer efficiency, designed to keep up with the increasing speeds of printers. These machines run any number of custom programs to cut, carve, and slice with laser-like precision.
Many manufacturers choose to incorporate these devices into their production lines due to the fact that they can produce high-quality results consistently and economically. Print service providers (PSPs) can add a standalone CNC router or work with an existing finishing device that might have a router tool as an option.
Above: Biesse offers routers capable of handling thick, heavy foamboard material.
Essential Tools
CNC routers offer print shops a digital method, with some unique benefits, to finish materials. Einar Ek, CAM solutions – pre-sales, Esko, argues that with CNC routers, print shops start offering new and exciting applications and capitalize on trends such as personalization and just-in-time production. The personalization advantage involves the ability to offer every sheet and/or cut differently to match specific customer needs.
CNC routers are an essential tool for print shops, as they run 24/7—if required—and can cut all materials accurately, consistently, and quickly compared to manual operations. They offer an efficient delivery time to customers, and even provide PSPs with the benefit of faster production throughput.
Either a cutter with a routing option or router with a knife option are alternatives, depending on the rigid materials used. “A cutter is a knife machine with a spindle option designed around high acceleration rate and motion. A CNC router is a spindle machine with option of a knife geared towards smooth motion cutting a high-density product,” explains Russell Boudria, router product manager, MultiCam.
“Adding routing capabilities to or purchasing them with a Zünd multifunctional cutting system significantly increases the range of rigid materials processed. The ability to say yes to jobs they would otherwise have to decline or outsource helps PSPs not just increase, but retain market share by giving them ultimate control over turnaround time and finishing quality,” adds Beatrice Drury, director of marketing and communications, Zünd.
Modern CNC routers from a supplier with a proven track record are easy to program, extremely reliable, and pay for themselves in a matter of months. They open up new business opportunities as well as streamline operations.
Current Trends
Steve Aranoff, international sales manager, Gerber Technology/MCT, says the biggest trend is suppliers of CNC routers addressing requirements from two different angles.
“The primary CNC router companies are adding better cutting technology and beefing up their software to handle print graphics and the cutter companies are strengthening their routing capabilities. The intent of both is to allow customers to do more with their cutting equipment,” adds Aranoff.
As the lines between print market segments continue to blur, the new normal for PSPs is to offer a full spectrum of products, ranging from retail promotional graphics, decals, and banners, to all types of displays, folding carton, and corrugated packaging. “Routing is just a part of this mix,” says Drury. “To meet this diverse range of finishing demands efficiently and profitably, print shops need specialized tooling and automated workflow automation.”
With the advancement of flatbed printers, according to Lance George, plastics division sales manager, Biesse America, there is a strong need for digital finishing—the process of digitally die cutting a printed sheet of material through the application of a camera system and software to provide accurate registration.
This trend is catching on quickly, along with the fact that CNC routers are becoming more versatile.
“AXYZ Trident machines are really hybrid router/knife systems, fitted as standard with a high-power routing spindle, as well as tangential and oscillating knife cutters. This makes them suitable for processing all materials that a modern print shop might use,” states Robert Marshall, VP market development, AXYZ International.
The use of modern tooling and machine drive systems and controllers is a trend that allows even higher levels of productivity and quality. Clear acrylic can now be cut to leave a polished finish, which eliminates the need for any post-production work. The benefits of this are huge for reducing lead times and minimizing costs.
Furthermore, when fitted with a camera registration system, routers accurately cut out pre-printed shapes with minimal operator involvement.
“Nowadays, Summa finishing tables are better equipped for contour printed jobs. The integrated camera system can read registration marks on many types of material, even reflective material. The interface is user friendly and a material database makes sure the best tool settings are always used. On the software side, flawless integrations are possible with almost any existing print workflow,” adds Barry Budwit, VP/GM, Summa America.
Average Cost
Depending on the size and options, tools, and other contributing factors, CNC routers can be between $50,000 to $140,000. Size, conveyor, modular head, workflow integration, and user friendliness are all topics to bear in mind.
According to Maureen Damato, sales dealer account manager, Colex Finishing, the standard Sharpcut 5×10-foot package that includes the triple interchangeable tool head, energy-efficient six-zone vacuum system, and Vision registration camera sells for $78,900 and this includes installation, on-site three day training, and one year warranty on parts and labor.
“The cost of a CNC router depends on the size and configuration of the machine. Typical prices for a good quality CNC router, reliable for ten to 15 years or more, can be anything from $30,000 for an entry-level machine to over $200,000 for a large, highly sophisticated system,” adds Marshall.
Learning Curve
CNC routers are used in a variety of applications, which make learning a long-term effort depending on your experience with computers and mechanical aptitude. Historically, CNC routers challenged users with complex user interfaces and set-up procedures. However, this is no longer the case.
“At Vision Engraving, we built a unique approach to make the learning process easier by breaking up training into application-specific courses. We offer online, on site, and on location training,” explains Mark deGuzman, marketing, Vision Engraving and Routing Systems.
George argues that two weeks of training is sufficient—including hardware and software training. After this, most users become more productive within a month of operations.
“Esko i-cut Production Console (iPC) offers an easy-to-use interface. Using its ‘shared resources,’ it stores the ideal settings for all the materials you work with. With user expertise safely kept in iPC, the setup procedure is done automatically. There are no more complex settings, as shared resources make everyone an expert,” says Ek.
CNC routers have much easier machine control and software capabilities than ever before. Modern programming systems are intuitive and guide a new user through the process. The easy part is training the operator on how to run the machine, which typically takes two to three days.
“The major differences have to do with how well the software capability integrates with the current workflow in use by the PSP. CNC routers tend to be easy to use for complex routing projects, but may not be fully integrated with the typical RIP, design software, or PDF workflows now common,” explains Aranoff.
According to Boudria, the print industry has driven the simplicity of operation to a very small learning curve.
Common Dimensions
Common dimensions depend on individual needs and what materials are to be processed. Most materials are available in standard sheet sizes and customers usually select a process area to match. Some PSPs may be limited by shop space but this doesn’t mean they can’t take advantage of a smaller machine.
George believes that most manufacturers provide a 4×8- and 5×10-foot table for digital finishing. The 5×10-foot table is almost always chosen because there is little difference between these two sizes.
In fact, most common for applications involving routing are bed sizes large enough to accommodate 4×8- and 5×10-foot boards, but it all depends on the shop’s production and workflow needs.
deGuzman agrees, adding that Vision also offers table sizes starting at 16×24 inches up 4×8 feet. “Our most popular CNC router is the Vision 2550, which has a 25×50-inch table size.”
Challenges to Overcome
With many rapid changes and advances in printer technology over the past couple of decades, print shops are under pressure to keep up with competitors by investing in ever-faster and more efficient digital presses.
Drury explains that these printer investments are often made without a thorough analysis of how added printing capacity affects the entire production workflow and, in particular, the need for cutting and finishing. This is especially true for jobs that involve routing, which may require multiple processing steps—for example cutting, polishing, and engraving.
“Meanwhile, PSPs also realize that the real price point differentiator comes from the complexity of their finished products, not the ink they print on a substrate, which further heightens the demand for more complex and time-consuming finishing,” adds Drury.
Besides learning curve, print shops need to keep in mind the importance of everything working in symphony. Budwit states the process of implementing a cutting solution is sometimes challenging but is proven to be a lot easier with the use of a RIP software to align the printer/cutter workflow better. Normally a dealer or a certified service technician assists in this process.
It’s important to understand which specific tools, features, and functions are required for an application too. Performance requirements are also essential to identify if the cutting capacity aligns with overall production.
“Keep in mind, each finisher has vastly different capabilities for each type of print material and the printed graphic, plus integration with other facets of the workflow. Buyers should make sure they test their own specific needs for both hardware and software integration to ensure they get what they really need,” explains Aranoff.
It’s critical to understand one’s entire process/workflow from when the order arrives until the invoice is sent out. It helps to identify and remove waste in the workflow. Many print providers underestimate this.
“At Esko, we offer a number of ways to reduce key waste areas. One, keep the press running. A proper workflow software will ensure that your press stays busy and not held up by a slow prepress process. Reducing reject rates from your printer are just as important,” recommends Ek.
Lastly, the machine may need to be situated away from printers to avoid the effect of dust or debris. Modern cutting heads with suitable pressure feet and a good extraction system can be extremely clean but there will be a small amount of dust that needs to be contained.
Main Tool Heads
With four basic tools you can pretty much cut anything—router, knife, crease wheel, and a kiss-cutting knife. There is a high need to be flexible and meeting your customers’ expectations yesterday instead of today. PSPs can buy tools/modules as demand increases for different material handling.
“Always have a basic spindle and a tangential knife. It is too narrow minded to just buy a router or knife cutter—there are too many materials and customer demands that you will lose market share if you were to have one or the other” recommends Boudria.
George suggests a spindle add-on for rigid plastics and aluminum. A tangential oscillating knife is ideal for foam-based board and thicker corrugated material. A tangential drag knife works well with film, thinner corrugated material, and paper stock. A creasing tool is helpful for packaging applications.
“A 3HP high-frequency spindle can do the majority of a print provider’s engraving or routing needs. There are also automatic Braille insertion tools, which allows for precise placement of Braille beads onto a Braille sign. This is essential for shops looking to produce ADA-compliant Braille signs,” explains deGuzman.
Add More Now
When a PSP has a need for printing to new materials, there is equal demand for new tools/modules that process the media. Some finishing devices are easily upgraded with the addition of a new tool head as customers’ needs change. Alternately, a standalone CNC router may be required. Overall, print shops need to determine what makes sense for them, their customer base, current product offerings, and their future goals for expansion or diversification.
Jan2019, Digital Output