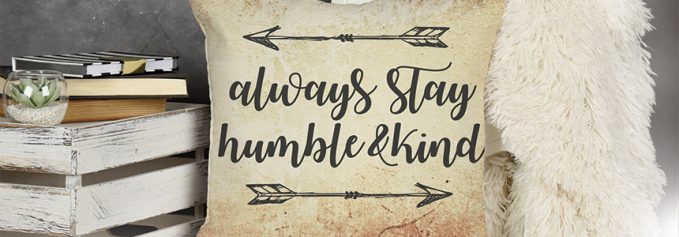
by Melissa Donovan
Digitally printed textiles are used in home furnishings. This includes everything from curtains and tablecloths to pillows and upholstered chairs. Each product has its own requirements based on where it is placed and how it is used in the home. Chair fabric needs to be durable, bedding linens must be washable, and curtains should offer some form of UV resistance to combat fading. To achieve these individual features, specific textiles as well as printing processes and ink sets are chosen.
Above: Potter’s Printing, with two locations in MA, prints its throw pillow collection using Fisher Textiles’ 1010 Element, a 100 percent polyester dye-sub printable fabric.
While dye-sublimation (dye-sub) transfer technology is the most well-known and commonly used across the graphics industry, other dye-based methods using pigment, acid, and reactive are highly sought after—despite the labor intensity that comes with some of these processes.
Opportunities to Furnish
The opportunity for print service providers (PSPs) already digitally printing textiles to expand into home furnishing markets is growing. Fueled by new introductions in hardware and media, interest continues to increase.
“The percentage of digitally printed home textile designs grows every year. Much of the growth is going to overseas print providers, but the converters that create the designs are strongly interested in producing product domestically,” admits Mark Sawchak, partner, PremEx Solutions.
Printer manufacturers and fabric producers respond to this growth accordingly. Marty Silveira, VP sales, DigiFab Systems, Inc., comments that printer manufacturers increasingly focus on providing equipment that handles both fabrics and inks suitable for home furnishing applications including pillows and cushions to floor mats, window treatments, lamp shades, towels, bedding, and wall hangings.
Enhancements to print technology raise the bar, allowing digitally printed fabric to achieve results similar to fabric printed with traditional rotary screen or flatbed pigment printing. “The introduction of more robust digital pigment printing technology for natural fibers and blends elevates the crocking, bleeding, and washability test results,” explains Mike Compton, product marketing manager, TVF.
Compton adds that the materials themselves also make digital printing’s presence grow in home furnishings. For example, the new, soft natural hand and feel together with the improved textures and looks of polyesters simulate natural fibers with the added performance that polyester provides, including benefits like stain prevention and soil release finish.
Reap the Rewards
Some PSPs are better positioned to add home furnishing items to their offerings. It depends on the technology already running in house as well as the desire to commit to a different market and customer profile.
Dye-sub transfer printing is a primary method used by PSPs printing soft signage and apparel, according to Compton. If this technology is in place and fabrics designed for dye-sub printing are used, it does make entry into the home décor market relatively easy for PSPs looking to diversify and add revenue streams to their print offerings, he admits.
“Depending on the end use, even PSPs that only use graphics-type pigment plotters could take advantage of fabrics and start producing pillows, curtains, and wallpapers. While home furnishings offer challenges of their own, some do not have as stringent wash or soft hand requirements. This allows existing PSPs to make commercial-grade products, oftentimes with the technology already in place,” agrees Hunter Ellis, president, Jacquard Inkjet Fabric Systems.
In addition to sublimation and pigment, Sawchak says there are opportunities for print providers with latex printing technology in house as well as direct to fabric capabilities including direct disperse reactive and vat dyes.
“The largest volume opportunities are available to print providers that have an ability to color match. There are also opportunities for some PSPs in less color-critical applications such as weddings and special events,” continues Sawchak.
Dr. Jerry Pinto, president, Fabachrome, believes that PSPs with an understanding of the home and hospitality markets for natural fabrics—which were traditionally printed with specialized reactive dye printers—are truly positioned to succeed.
Arnold Mekenkamp, BDM, Heytex, says creativity and the appropriate equipment to produce the finished product are also necessary. “This includes a further processing unit and perhaps even a well-equipped workshop.”
Numerous sewing facilities and upholsters cut, sew, and upholster products, shares Michael Sanders, director of printed textiles and finishing technologies, TVF. Outsourcing some of the process “allows PSPs to meet the ever-increasing demand for customized printed fabrics. They are able to deliver on demand customization with colors, styles, and individual designs.”
Dye Time
Choosing the right print process and ink for the fabric at hand is essential. Many types of textiles are used in home furnishings. Common dye-based processes for printing to textiles are pigment, acid, reactive, and disperse.
Pigment inks are the closest option to a one-size-fits-all approach. They are used on the broadest range of fabrics—cotton, rayon, linen, silk, and blends. “Pigment inks have many upsides. Simple products only require post-heat to fix, which attaches the ink to the fabric; however the color vibrancy is not necessarily the widest,” suggests Silveira.
Ellis believes pigments are at strongest when printed to natural fabrics used in applications that require lightfastness but not crockfastness or stringent washfastness.
Acid and reactive dyes each offer advantages. “Acid dyes are suitable for polyamide fibers, wool, and silk. Reactive dyes are water soluble and represent the largest dye group of cellulosic fibers, such as cotton, viscose, and linen. This is a permanent bond, resulting in particularly wet- and rub-resistant dyes,” comments Mekenkamp.
“The color range of acid and reactive dyes is very good and many properties like washability and crocking achieve high marks on the scale,” adds Silveira.
However, acid and reactive are part of a more complex print and finish process. Specifically referring to reactive dyes, according to Compton, “the fabrics require pre- and post-treatment. This includes steaming and washing to bloom color and remove unreacted dyes from the printed goods.”
Disperse dyes are common in the dye-sub process, making them suitable for polyester fibers and fiber blends. “High-energy disperse dyes are best for polyester home furnishing fabrics because they can achieve better lightfastness than low-energy dyes,” says Ellis.
Many PSPs offering textile printing in the form of soft signage use dye-sub, either direct or transfer. “Dye-sub is ideal because the print is sublimated into the fabric’s fiber. The best fabric for home furnishings is polyester or poly-blends because polyester is required for sublimation,” adheres Jeff Cheatham, director of product development, Fisher Textiles.
Compton argues that dye-sub heat transfer is the primary method of printing polyester home furnishing fabric based on ease of entry into the market.
Betting on the Best
Certain fabrics are favored for specific furnishing applications. To determine the best fabric for the job at hand, characteristics like durability and washfastness are considered, as well as the print process and ink.
Bedding fabric and linens are often constructed of natural fibers such as cotton, linen, rayon, and blends, notes Compton.
Ellis points out that bedding is washed regularly, so it requires a high washfastness and a soft hand is essential.
“Bedding requires stringent durability, particularly wash durability. Since cotton and polyester blends are common in this application, it lends itself to latex and pigment printing,” explains Sawchak.
Another category, linens—which includes tablecloths and placemats—are commonly compromised of linen, but can be made of polyester, cotton, or blends of the two, shares Silveira.
“Tablecloths are mostly poplins and soft knit fabrics,” according to Cheatham. “They require durability and stain resistant and/or waterproof properties.” Table linens should withstand repeated machine washing.
Upholstery fabric for furniture or throw pillows on the other hand is primarily cotton or cotton/linen, with some lower end furniture made of polyester, admits Sawchak. “Cotton-based fabric is popular due to durability and aesthetics.”
Upholstery and complementary throw pillows are typically woven or knit suede fabrics, adds Cheatham. “Upholstery and throw pillow applications require a durable fabric with great abrasion resistance.”
“Furniture has stringent specifications for crockfastness. For digital printing, cotton furnishing weight fabric with pigment and post-treatment is commonplace today,” shares Sawchak.
Window treatments, like curtains, drapes, and valances, are made up of polyester, explains Silveira.
This is particularly a textured polyester, according to Sawchak, in addition to cotton and cotton blends. “Curtains have less stringent durability requirements, though they need to withstand washing and/or dry cleaning. There may be a lightfast specification. This property is best addressed with pigment, latex, or in the case of polyester, high-energy direct disperse dyes,” he notes.
Treatment Thinking
Pre- and post-treatment for digital textile printing processes might be deemed necessary to ensure the dye/ink binds properly to the fabric. On the other hand, a treatment pre- or post-print can enhance important properties such as crockfastness, washfastness, or colorfastness.
“Pretreatment improves print quality and durability on every type of process except dye-sub transfer printing. Sometimes it is necessary and other times it is the difference between a vibrant print that lasts a long time and a dull print that fades after a few washes,” explains Ellis.
For example, if considering pretreatment based on the fabric, “it is critical for all cotton, rayon, linen, and silk fabrics,” advises Dr. Pinto.
“For cotton-based fabrics printed with latex or pigment, pretreatment is recommended. For reactive printed cotton fabric, a pretreatment of the fabric is necessary to help in the reaction between the dye and the fiber. After printing, the fabric needs to be post-treated by being steamed, washed, and dried to fix the ink to the fabric—as well as wash off the excess unfixed ink,” adds Sawchak.
Ellis adds that post-treatment for a fabric printed with pigment ink is a consideration when crocking is a concern.
Not all treatments are associated with properties like color, wash, and crocking. Certain applications might also require water repellency, anti-microbial features, or flame retardancy.
“Anti-microbial fabrics have a treatment to make them resistant to the growth of unwanted bacteria and other pathogens. Another option is a durable water-repellant treatment for stain resistance to help protect the fabric,” notes Cheatham.
“There are also UV-resistant post-treatments available. Many upholstery applications require a stain release, fire retardant, or other non-print-specific post-treatments,” adds Ellis.
Stunning Work
The application range for home furnishings is vast, including everything from furniture upholstery and throw pillows to curtains, tablecloths, and bedding. A PSP shouldn’t be wary of entering the space, but they should consider the many options and nuances. Identifying if existing print and ink technologies are suitable is the first step. If not, they are educating and purchasing the correct combination is important. From there, determining the intended product that the digitally printed fabric will be used for and coincidentally the textile type is next. Pre- or post-treatment considerations should be addressed.
Each step influences the other. When effectively performed from beginning to end, the result is a stunning piece of furniture, a custom curtain, or specially produced tablecloth. DO
Jul2020, Digital Output