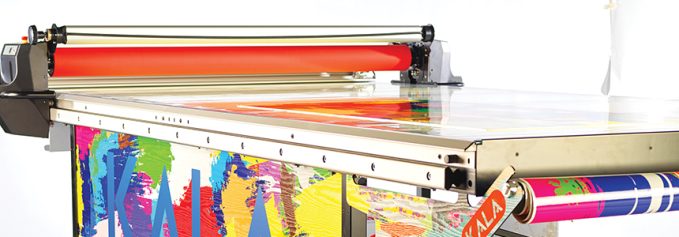
By Cassandra Balentine
Flatbed applicator tables help improve productivity in wide format print environments. For some, an investment in one of these handy pieces of equipment can take the place of an additional employee. These unassuming machines assist in mounting digital prints, pre-masking, lamination, and also serve as workstations.
Flatbed applicator tables offer a simple solution for the daily challenges presented in sign making. “The excellent functionality is powered by the idea of facilitating and streamlining the multiple tasks encountered in the daily work of sign makers, regardless of media type such as self-adhesive vinyl applications, application tape, laminations, road signs, glass applications, or banners,” shares Svein Ove Martinsen, VP sales and marketing, Rollover AS.
In addition to the benefits they offer in terms of productivity, they are simple to use and require minimal resources to operate.
These devices also help accurately and confidently register and mount decals to large substrates with little labor requirements, offers Brian Gibson, wide format specialist, GBC SEAL.
“They are simple to use without extensive operator skills. They serve as worktables for cutting and weeding and bring versatility to the workshop,” agrees Frank Romanello, VP sales, KALA Finishing Systems Inc.
Above: KALA Finishing Systems’ AppliKator roller is made of high-resistance silicon, not rubber. Adhesive materials won’t stick on its surface for easier operation and less waste.
Easy Investment
As implied, for sign makers that do a lot of mounting in house the benefits offered by flatbed applicator tables are clear.
“The fact that a flatbed applicator enables major finishing jobs to be done in minimum time, often involving half the manpower, makes them literally pay for themselves quickly as well as offering better working conditions for the operators,” shares Ove Martinsen.
Romanello points out that comparing the manual application of prints with a squeegee onto a rigid surface is cheaper in terms of investment, but is simply not as profitable as investing in a laminator or application table.
“Mounting a print on a board can be achieved by various methods. Based on a study performed by a large sign shop in America, mounting a ten-foot long print to a board takes one operator approximately one minute and 20 seconds with an AppliKator table, two minutes 20 seconds with the Mistral laminator, and six minutes for two people applying it manually with a squeegee,” offers Romanello.
An investment in a flatbed applicator ideally leads to more work capacity, improved production flow, and minimizes errors and wastage, says Gibson. “It is a work bench for speedy processing of all varieties of projects, not just laminating and mounting,” he adds.
With a flatbed applicator, there is better control of the laminating process. “Side trays and media holders/dispensers keep graphics clean and away from dirt and debris. Flatbed applicators are also ergonomically efficient and easy to operate,” shares Gibson.
When it comes to investment, Ove Martinsen points out that there is an extensive range of model sizes, so the cost would be closely connected to this. “A normal size shop will need a model from $15,000 to $25,000,” he estimates, noting that there is no maintenance beyond keeping it clean.
Romanello says pricing starts at $14,250 for two-meter tables. “With our tables being modular/expandable, the price would be determined by the length the customer needs. The surface cutting mat is a consumable item and needs to be changed once both sides are consumed. Keeping your table clean and free of debris assures continued performance and consistent output.”
With investment costs under $17,000, Gibson says flatbed applicators add production flow process to the work area. “Very little to no maintenance is required and they work right out of the box with a two to under three hour set up time.”
Target Market and Demand
Sign shops with a big demand for mounting projects are ideal candidates for an applicator table.
“Sign makers make up the vast majority of flatbed applicator customers, as the properties fit right into their daily tasks,” asserts Ove Martinsen.
“The target market is sign shops with volume mounting projects,” agrees Gibson. A flatbed applicator table is a great investment for various projects like cut vinyl graphic masking, quickly applying security film to boards/substrates for transportation protection; wherever there is a need to accurately register graphic panels whether laminated, unlaminated, or not mounted; manufacturing where security/scuff resistant films are applied post manufacturing; and graphic production shops requiring a work bench and efficient production flow.”
Romanello says sign shops, photo labs, reprographic shops, traffic signs fabricators, and any type of business that performs a lot of mounting onto rigid substrates and application tapes would most benefit from a flatbed applicator.
Print providers use a range of materials in association with flatbed applicator tables, from self-adhesive vinyl to boards, flexible substrates, laminates, application tape, and vinyl, explains Ove Martinsen.
Rigid items like foamboard, aluminum composite material, acrylic, wood, expanded PVC, and other smooth, flat rigid board up to two inches thick are also supported, notes Romanello.
Limitations
Like any equipment, flatbed applicators have their limitations. For example, when it comes to laminating long runs of vinyl, Ove Martinsen admits the process may be achieved better with a roll-to-roll laminator.
“Determined by the volume of the type of jobs your shop produces, one may want to consider what piece of equipment can make you the most money,” recommends Romanello.
Footprint is another consideration, says Gibson. It is important to determine the largest average size that must be handled. For example, vehicle wrappers may want to consider a roll laminator for production lengths beyond the length of the table. Tables range from ten up to 34 feet in length and can be from 63 to 80 inches wide. “Will your flatbed fit your current location or will you have to move?” he asks.
Learning Curve
Flatbed applicator tables present ease of use in a number of ways—and this even includes the setup process.
“The use of a flatbed applicator is pretty much self explanatory and requires no special experience or skills beyond what is available from our manuals and videos,” notes Ove Martinsen.
Romanello shares that a new operator can be fully trained in less than 30 minutes.
“The learning curve is minimal, as most operators are proficient after a few minutes. There are a lot of videos on YouTube depicting how to use a flatbed applicator table. The typical learning curve is 30 minutes to one hour,” agrees Gibson.
Flatbed Applicators
Flatbed applicators are a great addition to any sign making business. They offer increased productivity, are easy to use, and require minimal maintenance.
Jul2022, Digital Output