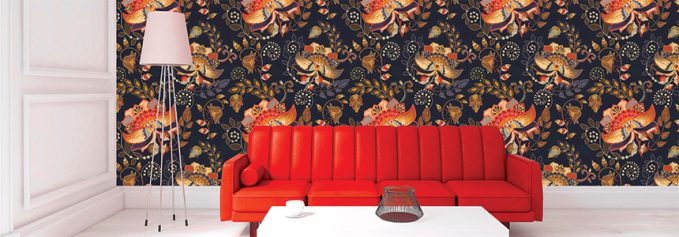
By Olivia Cahoon
Roll-to-roll (R2R) printers are well equipped to handle the needs of digitally printed wallcoverings. Available in a variety of sizes, these devices run several ink sets and offer media handling features ideal for consistent wallpaper feed and take-up.
Wallcoverings are found in corporate offices, homes, hospitals, hotels, retail stores, and sports arenas. Their growing popularity presents opportunity for print service providers (PSPs).
“Many sources in the market estimate that digitally printed wallpaper is anticipated to reach 10.43 billion USD by 2025,” shares John David Kaufman, specialist, marketing senior, Canon Solutions America. According to a recent Energias Market Research report, primary factors driving market growth include rapid urbanization, increasing demand for digital technology in wallpapers, and growing capital investments in research and development.
As the wallcovering market expands rapidly across the U.S. it’s also making waves in Europe, comments Luis Garrido, director of equipment, an authorized Polaroid licensee, Polaroid Large Format. “We are seeing custom printing not only by corporations applying their logos and statements in their offices, but also growth in the home décor and interior design industries.”
Above: The Canon Colorado 1650 with UVgel and FLXfinish technology delivers productivity to meet the demands of wallcovering production.
Does Size Matter?
Roll printers from 20 to 126 inches are used to print wallcoverings. In this market the most popular R2R printer sizes include 20, 38, and 54 inches. While maximum print width is essential, most wallcoverings are produced on devices in the 38- to 54-inch range to accommodate handling during installation.
Handling and installation are important considerations for printing wallpaper. PSPs should factor in the logistics of not just production, but also installation. “In some cases, the width of the printer can often be less important,” reveals Dan Johansen, senior marketing manager, commercial and industrial printing business, Ricoh USA, Inc.
For example, installers need to lift and handle material to apply the panels. As a result, Johansen says most installers prefer 36- to 48-inch widths based on their average wingspan. Due to this natural limitation, he believes printer size doesn’t matter as much because the ideal width of each panel tends to be narrower than most devices used.
To determine the best roll printer for wallcoverings, Mark A. Rugen, director of product marketing and education, Mutoh America, Inc., suggests PSPs consider the number of required installers. “The more people, the wider a print you can install in many cases,” he explains.
For example, a standard 21-inch wallpaper typically means there will be seams. Rugen says PSPs can minimize seams by using a 48-inch or wider printer and having enough staff to handle it.
Since wallcovering material usually comes in narrow rolls it’s important that the roll printer processes the roll size efficiently. Therefore, for a larger R2R printer, a dual roll option helps keep the output for narrow rolls as high as possible, comments Mike Kyritsi, president, swissQprint America.
Traditional wallcovering rolls are available in 21- and 27-inch widths making printers in the 54-, 64-, and 126-inch width range typically do well, shares Tom Wittenberg, events and industry relations manager, HP Inc. Because digital printing offers more flexibility for print widths, limitations are typically associated with available media widths. “Even then, the printer sizes mentioned can still do the job nicely and provide more flexibility than the standard analog wallcovering printers.”
Wallpaper is usually installed in sections that are 20 to 36 inches wide. Once the media size and width of each panel is determined, the decision to print one-, two-, or four-up or dual rolls is made, shares Jason Darrah, chief inkjet evangelist, Fluid Color LLC.
Determining Ink Type
Several ink types are used in the production of wallcoverings such as latex, solvent, water-based, and UV. Solvent inks were traditionally more suitable to produce wallcoverings on roll printers due to their permanence. However, this required pretreatment to prevent the solvent ink from degrading or weakening the material composition.
“This made wallcovering materials more expensive to produce,” adds Michael Maxwell, senior manager, Mimaki USA, Inc. As a result, alternative ink technologies became more attractive such as latex and UV-curable.
Latex ink offers a smooth, level surface that preserves media appearance. It’s also particularly suited for wallcoverings because of its no-odor factor. “With competitive technologies, there will be a lingering odor for days or even weeks after installation,” offers Wittenberg.
However, Maxwell warns that latex inks are more susceptible to failure when the wallcovering is introduced to cleaning agents or sunlight because they are water-based and the ink sits on the material’s surface.
While UV-curable was traditionally too rigid for this type of application, recent advancements in UV-curable ink technology are quickly gaining popularity. “UV inks now have enough pliability and durability to withstand the stresses of high-traffic environments,” explains Maxwell. Although UV ink is still not as durable as solvent, he believes it is significantly more durable than latex.
Larry D’Amico, sales director, North America, Durst Image Technology US, LLC, agrees and says UV ink’s durability, consistency, and media flexibility are the best fit for most wallcovering applications. “One critical element where UV excels is the ability to produce consistent results through a print run,” he explains. “It is critical to any wallcovering application that the output from beginning to the end has little or no color shift.”
UV ink is also popular because UV LED curable printers produce less heat with cool LED curing, which doesn’t cause media deformation. According to Darrah, high temperatures and material distortion can affect each panel’s print length causing registration issues during installation.
“If the edge-to-edge registration doesn’t fit perfectly, the installation process can be very complex and take up a lot of time,” agrees Kyritsi.
As with many applications, technical problems encountered while digitally printing wall décor can be traced directly to the pros and cons associated with current ink technologies—latex, eco-solvent, and traditional UV. “No single available option checks off all the boxes,” adds Kaufman.
Media Handling
Media handling is essential to produce digitally printed wallcoverings accurately and consistently. The most important media handling features for roll printers producing wallcoverings include consistent feed units, linear consistency, and accurate alignment.
Since most wallcovering jobs are custom, there are fewer long runs. As a result, Wittenberg says ease of media change out and setup times are critical for manufacturers in this business as substrates change regularly—even for each run—and setup times need to be kept to a minimum to keep costs down.
“Productivity can be severely limited if you frequently need to stop a printer to modify or re-center,” agrees D’Amico.
Linear consistency is one of the most important factors. According to Johansen, consistency makes all the difference in image quality because wallcoverings tend to be printed in tiles or panels that may require seaming with no overlap.
Accuracy in advancing media and in printing is also important for success. Since wallcoverings are installed edge to edge, Kyritsi says the individual parts of the larger image must align perfectly to each other. R2R printers offer features for high accuracy such as sensors and control systems that continuously keep optimal tension in the rolls.
Media handling features should also be considered based on whether the PSP is printing rolls or wallpaper sheets. “Either way, it certainly is important that the media be fed without skewing and that it be dry to the touch after leaving the printer,” offers Rugen.
Additionally, when using a latex or UV-curable solution, Maxwell says it’s important to choose a printer that generates minimal heat. “High heat environments can distort the material and degrade its structure.” UV LED printers offer a viable solution due to the low heat curing lamps.
Common Substrates for Wallcoverings
Several hundred substrates are used for digitally printed wallcoverings including fabric, film, foil, non-woven, paper, PVC, PVC-free, and textiles. Therefore, determining the proper substrate should first be based on the printer and ink type.
“The wallcovering substrate manufacturers have all developed lines of media that are compatible with the different digital ink technologies,” comments Wittenberg.
While traditional PVC films are often used it is increasingly common to see digitally printed, fabric-based wallcoverings. “They give the look and feel of traditional wallpaper and new adhesive technologies reduce the need in many cases for complicated gluing processes,” shares Maxwell.
In the interior décor market, printing wallcoverings for offices and homes is typically a state-of-the-art process that involves creativity from designers, architects, and interior designers. Depending on the project, Garrido says they may choose to incorporate textures for a preferred effect. To do so, common substrates include paper and textile wallcoverings such as canvas.
Textured wallpaper and adhesive-backed options are often used for design aesthetic. Rugen believes this is ideal for locations requesting wallpaper murals rather than repeating designs. High-heat devices may not be compatible with some of these specialty substrates, making UV LED printers a good choice.
According to Kaufman, vendors also provide PVC-free wallpaper and wallcovering options that are more environmentally friendly and allow contractors to earn LEED credits. GREENGUARD Gold and Type ll certifications are important, and in many cases are required for wallcoverings used in daycares, schools, hospitals, and other public places. Peel-and-stick media options are increasing in availability and presence for do-it-yourself jobs and short-term installations.
Before selecting a R2R printer for wallcoverings, PSPs should ensure the device offers substrate compatibility. For example, wallcoverings for commercial and industrial applications tend to be thicker. According to Darrah, printers with the ability to raise the printhead carriage to accommodate this reduces the likelihood of printhead rubs and strikes.
Instant Drying Features
With increased competition in U.S. and international markets, time is a crucial part of the print business. Instant drying features allow PSPs to reduce error, shorten turnaround time, and increase revenue when producing printed wallcoverings.
“Every vendor or customer wants their finished work now if not yesterday,” shares Sohil Singh, VP, StratoJet USA. With such high competition, instant drying is a critical need for every wallcovering business.
Instant drying provides the ability to immediately handle printed materials. “It is a convenient feature and it allows designers to immediately check that the prints align with expectations,” comments Garrido. Instant drying also reduces the likelihood of damage during the drying process.
Finishing a wallcovering relies heavily on instant drying features. For example, Kaufman says other technologies producing digital wallcoverings typically require lamination, and if the ink is not degassed or fully cured—you must wait to do so. UV inks that do not require lamination reduce waste and increase profit for PSPs.
Wittenberg believes the fewer steps in a process and the less dry time means more money in the PSP’s pocket. “Instant drying is key to reducing not only costs but cycle times as well, allowing a faster response to the customer.”
In high-speed R2R printing, Darrah says instant drying features are critical because there is limited time for drying before the wallcovering is rolled up on the take-up roller.
“Instant dry features such as those offered by UV-curable printers create an opportunity for PSPs to produce wall graphics for any environment in real time, and offers the capability of quickly responding to reprint requests due to installation failures,” agrees Maxwell.
Targeted Software
Both RIP and layout software support roll printers and are beneficial for PSPs creating wallcoverings. Depending on the solution, programs are available for patterning, tiling, and importing.
Generally, all RIP software includes features that assist with wallcoverings, such as editing layout, tiling, and multi-print. This allows for faster designing and print file generation as well as increased control on the final output, shares Singh.
To select the right RIP, determine how user friendly it is for creating, editing, tiling, or modifying final designs, and in some cases correcting colors. “A lot of users also like to check the rendering speed per file, as it’s important for wallcovering applications due to the large file sizes and it helps in saving time,” offers Singh.
According to Johansen, image tiling and printed overlap programs are especially beneficial and help ensure installers can properly marry edge to edge as they install each panel across a wallscape. This prevents the need for reprints and saves time on installation.
RIPs with the ability to step-and-repeat patterns from a single element help in design. Pattern repeating as well as mirroring and offsets provide designers with a variety of choices for pattern making. The RIP should also allow importing or compatibility with numerous design packages for wallpaper, says Rugen. “Some RIPs may allow for color changes in the pattern right from the RIP, adding additional design capabilities for the artist.”
In With the Popular
As wallcoverings continue to grow in popularity, now is the time for PSPs to take advantage of the booming market. Before selecting a R2R device, it’s important to consider a print width capable of handling the shop’s targeted media roll size. Ink type is also crucial as it effects the wallpaper’s durability, substrate selection, and dry time.
Mar2020, Digital Output