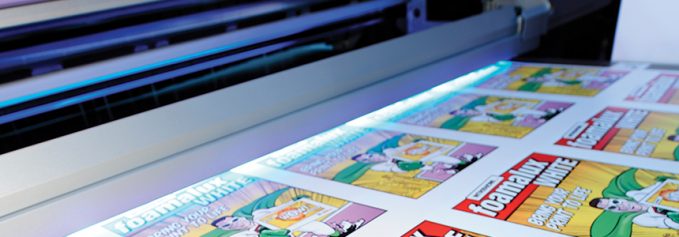
By Cassandra Balentine
PVC-based rigid board materials are popular for direct digital printing. Evolving from the role as a backer substrate, the latest wide format printing technologies expand the use of these materials. As such, manufacturers of rigid PVC board continue to advance product lines to meet changing demands.
There are a variety of considerations to take into account when shopping for PVC board for digital printing. “All foamed PVC boards are not created equal. When selecting a PVC board, graphic designers and fabricators need to compare the physical properties, manufacturing processes, and tolerances of competitive products,” says Doug Twitchell, senior regional sales manager, 3A Composites USA. He adds that in direct printing applications, a tight thickness tolerance is essential. “Thickness deviations from sheet to sheet not only affect ink spread and appearance of the printed graphics, but can result in costly printhead strikes,” he shares.
Advancements in weight, durability, color choices, and supported ink sets continue to drive the use of rigid PVC substrates in digital print environments.
Above: Brett Martin’s selection of bright white Foamalux White is available in a range of thicknesses from one to 24 mm and three difference widths.
Historical Usage
The use of PVC board substrates has evolved over the past several years. Michelle White, technical applications manager, Vycom Plastics, says PVC board was historically used as a backing substrate. “Roll-based media, such as self-adhesive vinyl, would be imaged and then applied to the PVC board for rigidity. Digital flatbed printers changed that usage dramatically by enabling print service providers (PSPs) to directly image to a board.”
Duncan Smith, sales director, Brett Martin Plastic Sheets, explains that PVC foam sheets were originally screenprinted and used as a substrate for vinyl. “In the last 15 years, since the advent of flatbed digital printing, PVC foam sheets can be digitally printed direct.”
PVC sheets are commonly utilized for retail applications and trade show signage. “Within the retail space, they are primarily used for signage and display applications. Typically, brand and logo identification or directional signage, but sometimes as a printed backer board for shelf and aisle end caps. The trade show industry uses PVC mostly for header boards and display signage. PVC also carries a fire rating preferred by retailers and trade show installers,” adds Tony Lampariello, national rigid media manager, Agfa Graphics.
Mark Six, technical product manager, The Mosaica Group, says PVC is widely found in indoor and outdoor signs, retail, point of purchase (POP) displays, and trade show displays. “Because it’s so dense and water resistant, it can be routed, cut, bent, and heat bent into a variety of sizes and three-dimensional shapes. PVC can also withstand the harsh elements of the outdoors better than other media. PVC boards range in thickness from one to 12.7 millimeters (mm), but can be produced up to two inches thick. However, this thickness is not common. PVC board is ideal for digital and screenprinting.”
Recent Advancements
Many PVC board manufacturers are introducing updates to their product lines. New features include brighter white points, lighter weights, added color options, and improved durability.
One of the latest advancements in PVC media is co-extrusion, which is a process that results in a white/black PVC material, shares Lampariello. Also, multi-layered PVC recently hit the market creating a white/black and white/black/white material. This technology allows PVC to be cut, scored, and folded. “This was not possible within the standard extrusion process of making PVC,” he continues.
White says some PVC substrates are now formulated with bright white surfaces to deliver vibrant colors and highlight cooler tones. A consistent brighter white point is a major consideration for applications where color reproduction is essential, such as POP displays or color-critical applications.
Smith explains that the majority of PVC foam is processed using flatbed digital printing. This has increased the importance of a smooth matte surface without defects or a rough grain. “The whiter the substrate the brighter the end color of the ink. The majority of PVC foam is used indoors as aluminum composite has replaced PVC for outdoor applications. This means PVC foam does not need to be as heavy, thick, or as durable. Savings due to weight can be spent on increasing the quality of the surface for printing,” he adds.
Sintra-based PVC products evolve with technological advancements in the printing process. “Sintra was first introduced for screenprinting in which thick, heavy inks covered surface irregularities. Today’s digital printing processes utilize much thinner, translucent inks that require improved surface consistency,” shares Twitchell. He explains that there is less tolerance for extrusion lines and flow. “Today’s Sintra is manufactured with more concise surface characteristics. It is a natural evolution for the product as printing processes evolve.”
Many PVC boards are lighter weight than previous generations, points out White. This helps reduce shipping costs without significantly sacrificing handling properties.
According to Brett Thompson, sign and graphic market manager, Piedmont Plastics, “light weight” tops the list of advancements. “Manufacturers have been grappling with ways of making their sheet more competitive with foam and paper products. Virtually every brand has an economy option that is less dense and geared for short-term applications.”
“Recently, less dense, lighter weight, and less expensive products dominated. The denser, harder, expensive products are used less—even though many people say they prefer a denser product, they do not want to spend the money for it in many cases,” explains Six. The lighter weight product is just as good for interior applications, whereas for exterior purposes, it may not be as durable for the outdoor elements. “It tends to chip more during routing and cutting,” he cautions.
Wade Sisco, director of marketing, United Industries UltraBoard, says there have been a few changes in recent years. “Most—if not all—PVCs were lead stabilized in the past. Now, most—if not all—are tin stabilized,” he offers. Additional changes include reduced density PVC substrates and the availability of brighter white points.
Color Considerations
While a white foam product is most common, PVC board manufacturers also offer varied color options.
Smith says white, followed by black represents 98 percent of the PVC foam market. “Colored PVC foam sales have reduced since printing any required color is simple with flatbed printing. Use of cut vinyl lettering on colored PVC foam has also greatly reduced.”
“PVC manufacturers have kept it simple over the years,” admits Lampariello. Standard colors include red, blue, yellow, green, light gray, dark gray, black, and white. Customer colors are possible, but high minimums apply. High density polyethylene sheet (HDPE) material has the capability of being made in versions like blue/yellow/blue, green/white/green, yellow/red/yellow, and blue/yellow/blue, but these materials are not printable. They are typically used in recreational applications like playgrounds and ice rinks.
Six says a majority of distributors only stock white and black. The Mosaica Group can provide most other primary colors within a week or so. “We offer a co-extruded black PVC foam board with a white facer.”
“Typically, sign printers will print colors to the substrate, unless the client requires a massive run for a large campaign. Larger, commercial-oriented runs may justify sourcing a colored PVC, but mass run setup costs versus ink cost ratio must be sustained,” explains Sisco.
Marina Batzke, GM, American Permalight, Inc., adds that photoluminescent rigid PVC has a soft yellowish daylight color. “Once all building lights are out, the rigid PVC surface has a greenish-yellowish color. This color wavelength can be perceived very well by the human eye in full darkness, making photoluminescence ideal for emergency evacuation signage.”
Black Core PVC
Furthering on the discussion of color, the use of black core PVC material is trending in the wide format digital print space.
Black core PVC material is a growing market. “Photographic art was the initial application for black core PVC. Routing the white surface and exposing the black core has created a wider range of creativity and design,” explains Lampariello. This process can be standalone while incorporating the different elevations of PVC and using black and white for visual focus points. The multi-layered PVC allows the cut, score, and fold features to be used in kiosks or printed displays that act as a structural unit and showcase products.
White sees interest in multi-layer PVC sheets, which comes from PSPs that want to utilize the white surface for printing color—rather than using white ink on black surfaces—and want the aesthetic appeal of a black edge. “Co-extruded HDPE material is also beginning to get noticed for outdoor wayfinding and signage applications. This is because, when routed, it offers a contrasting interior color,” she suggests.
Six says the black core against a white wall adds dimensionality and looks like a finished edge without some of the costs that this typically produces. “This is a relatively new product that up until recently was not available on a regular basis. Ideal applications are POP displays and inexpensive décor artwork,” he recommends.
While surface color options have always been important, Twitchell believes there is an increased interest for Sintra boards featuring a black core—especially for wall-mounted displays. “The black core seems to almost blend into the wall. It also helps to maintain the display’s attractive appearance longer because the black core doesn’t show dust on exposed edges—especially in denser thicknesses.”
Sisco notices a steady increase in PVC board with black core. “The white/black/black color combination may be more ideal because printers do not need white ink capabilities for printing to black facers, as well as providing a more subdued core and backer color in contrast with the printed art on the white facer.”
He adds that color combination selection may be more dependent upon the final desired aesthetic. “What is the color scheme of the environment? Does the client want the signage to standout or be more subdued?” An example of this would be using white core for an art gallery exhibition where the gallery walls are white. Using a black core would cause a higher contrast with the white environment and attract visitors’ eyes away from the artwork. However, an installation in a coffee shop would lean towards a black core, as coffee shops tend to have darker color schemes and the black core would blend.
Smith sees increased interest in white/black/white products as well. “Clients appreciate the black edge on a print, giving it the photo mounted gallery look.”
On the Market
Several companies offer rigid PVC boards, each with their own features.
Sintra PVC graphic display board by 3A Composites was introduced more than 30 years ago to the Americas. The company offers Sintra Bright White and expanded its PVC boards to include much wider thicknesses. Sintra is available in a range of thicknesses and colors from one to 12.7 mm. The company recently introduced Sintra ECLIPSE in its PRO Series line of graphic display boards. It is comprised of moderately expanded PVC in a homogenous black sheet with low-gloss, thin white PVC on one surface that is specially designed for screen and digital printing applications.
Agfa offers Duratex Foam PVC white three and six mm in white and black. The company also offers a co-extruded Duratex Foam PVC in white/black in three and six mm and a ten mm in white/black/white. The new Duratex Multi-Layered Foam PVC material comes in white/black/black and white/black/white in three and six mm.
American Permalight UL1994-listed rigid PVC sheets are printed with solvent- and eco-solvent based digital inks, allowing PSPs to custom print staircase identification signs for high-rise buildings where each sign has a different floor number and changing evacuation information. A number of different code and requirements for Photoluminescent Safety are applicable in the U.S. American Permalight offers several grades of rigid PVC that are UL1994 listed for Egress Path Making signage and even UL924 listed for exit signs, fulfilling the stringent requirements of the brightest building code applications.
Brett Martin provides a range of PVC foam substrates. The company’s selection of bright white Foamalux White is available in a range of thicknesses from one up to 24 mm and in three difference widths, in high- and low-density variations. It produces a line of Foamalux Colour in three and five mm with 16 colors standard and offers color matching to specific Pantone requirements based on minimum order quantities. The more environmental Foamalux Xtra product features a recycled black core and is available in thicknesses from three to 19 mm.
The Mosaica Group offers the Achieva PVC board product line. The company has the ability to stock 4×8-foot up to 60×120-inch sheets and is able to obtain color sheets relatively quickly. It carries the co-extruded black PVC foam board with a white facer.
Piedmont Plastics offers PVC board at all of its locations in a variety of colors, thicknesses, and sheet sizes.
United Industries offers UltraBoard Plus, which features a foam core versus a solid PVC core. The foam core increases rigidity by layering adhesives and facer/core materials. In addition, the lighter board is ideal for reducing shipping costs while retaining durability.
Vycom offers premium signboard solutions. The high-density construction ensures clean edges after cutting or routing, eliminating the time consuming step of manual deburring. The substrate’s surface promotes superior ink adhesion, reducing chipping or cracking after cutting, which can lead to substrate and ink waste and enabling an increased yield of sellable prints. Consistent craftsmanship in manufacturing ensures PSPs always receive sheets with dependable quality. The bright white point of Celtec Vivid White sheets deliver vibrant color reproduction tones to produce images that come to life.
Tried and True
PVC boards are found in a number of digitally printed, wide format applications. While they have been used for decades, advancements in flatbed digital printing have opened up new markets and applications for this substrate.
Feb2019, Digital Output