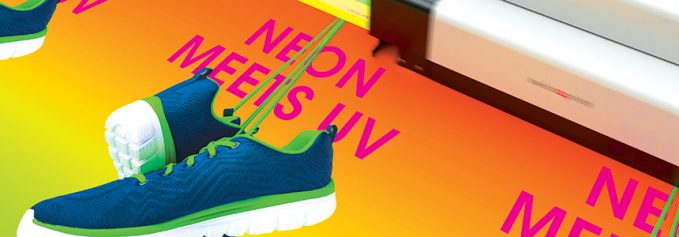
By Melissa Donovan
The introduction of UV ink was a pivotal milestone for digital printing. UV ink and the iterations that continue to follow open the door to a number of possibilities not once thought possible. Pairing advancements in curing technology with ink chemistry leads to a greater number of substrates printed to directly, as well as ink configurations offering less-harmful odors, higher viscosities, wider color gamuts, less fading, and more durability.
It is no surprise than that in MarketandMarkets’ Large Format Printer Market by Offering (Printers, RIP software, Services), Ink Type (Aqueous, Solvent, UV Curable, Latex, Dye Sublimation), Printing Technology, Printing Material, Print Width, Application, and Geography – Global Forecast to 2025 report, the research agency cited the market for UV-curable ink-based large format printers to grow at the highest compound annual growth rate during the projected period.
“The growth can be attributed to the numerous advantages provided by UV-curable inks, which includes but is not limited to; the ink dries almost instantaneously because of its high density, is UV resistant, and does not have any significant environmental impact. This makes it durable and suitable for printing on a wide range of flexible materials, along with rigid substrates such as wood and metal for direct print. Therefore, the UV-curable ink is increasingly replacing solvent ink despite being expensive owning to its added benefits,” according to the study, which was published in April 2020.
Above: The swissQprint UV-curable, acrylic-based FS1 Neon inkjet ink series brings the glow of neon colors to inkjet printing.
UV vs. UV LED
There are a number of differences when it comes to traditional UV versus UV LED ink, however the largest involves curing. As is the case with any technology, it was understood rather quickly that despite the positives that UV presented to the print space, it could be improved. The advent of UV ink acted as a stepping stone for chemists to achieve the UV LED ink configurations we know of today.
“Early UV inkjet printing technology used high-heat UV lamps to cure the ink properly. The traditional lamps consumed more energy, had longer heat up times, and could not print on heat-sensitive materials. When LED technology was introduced, it significantly reduced power consumption, eliminated wait times, and offered more versatility to print on a broader range of substrates,” explains David Lopez, product manager, Professional Imaging, Epson America, Inc.
Lack of heat is one of the reasons UV LED ink is compatible with a wider breadth of materials. “Conventional UV lamps produce a lot of heat, which in turn can have a negative effect on the exposed substrates. Most notably, it can cause some material to warp while printing and UV LED does not,” shares Syd Northup, VP sales, digital US, Marabu North America LP.
“Another advantage of LED versus mercury is that LED lamps do not degrade over time. If they’re lit, they’re putting out the same intensity that they did on day one. Conversely, mercury lamps degrade over time without any indication. Unless you invest in tools to measure lamp intensity, you could end up with curing issues without knowing why,” continues Northup.
Flavio Ronchini, CEO, Epta North America, agrees that at present, UV LED lamps “have virtually supplanted old mercury vapor technology.” To satisfy users of both curing methods, Epta is developing a product that could be used in either technology. “Since the frequency range of LED lamps remains narrower, photoinitiators are chosen with the certainty that they will be fine even on traditional UV lamps.”
Marc D. Baumgartner, purchase manager and Marco Eicher, ink laboratory manager, swissQprint, believe the limited number of usable photoinitiators is a disadvantage to UV LED and it is because of this that “the ink’s curing takes a lot of expertise.”
Photoinitiators are an essential part of an ink’s chemistry. “We have the ability to increase the photoinitiators to tune them to specific wavelengths for LED. This increase of photoinitiators allows for the heating of a specific substrate, lowering costs and promoting better adhesion,” explains Northup.
“UV LED gives us the possibility to adjust the curing settings to achieve good adhesion on different media. This is one key advantage compared to the former mercury lamps,” adhere Baumgartner and Eicher.
While UV LED features a lot of positives, traditional UV ink is still what it was built off of, and thus many of the advantages originate from it. “UV LED technology affords you the fast speeds and outdoor durability that conventional UV is known for,” explains Derek Moffett, product manager, Mutoh America, Inc.
“The most obvious advantage of conventional UV curing in terms of ink design is the latitude it affords with respect to chemical component choice due to the broad spectrum of UV emission. Having multiple peaks across the UV part of the light spectrum means ink designers can choose from a variety of photoinitiators to catalyze the polymerization process. Essentially, broad spectrum UV allows for more flexible ink design and better surface curing in general,” explains Jeff Edwards, senior business development manager, Americas, Canon Production Printing.
Conventional UV or UV-curable ink is a more aggressive chemical configuration, which allows it to bond to a greater surface area. “These inks cure differently than UV LED inks, and thus have a bonding agent that contributes to those differences. UV-curable inks need a more powerful light source to cure. Inherently, that light source is also hotter, and therefore more expensive to run. Substrates printed on with UV-curable inks also tend to bubble, buckle, yellow, and wave, however, adhesion can be better on substrates not affected by the lamps,” admits Jay Roberts, UV printer product manager, Roland DGA Corporation.
“I do not see conventional ink as necessarily having a disadvantage—besides conventional UV typically consuming more energy, but more of a different application potential, especially when formulated to be high adhesion,” argues Ramona Serafino, product marketing manager, Fujifilm North America Corporation – Graphic Systems Division.
Lower Viscosity and Odor
A notable development in UV ink chemistry is lower viscosity and lower odor features. Advancements in viscosity are important as they relate to ink jetting from the printhead, which directly influences image quality. Improvements in odor are sought after to address issues related to placing digitally printed pieces in sensitive environments.
Image quality is connected to ink viscosity. “The ability to have a lower viscosity ink allows for a more stable and precise ink dot ejection during the printing process. Optimal control of the dots directly affects the smoothness and quality in photographic images,” explains Lopez.
Precise ink dot ejection translates to smaller dot size. “The smaller dots allow printer manufacturers to utilize the full capabilities of the latest printheads to produce higher resolution prints,” says Northup.
“Lower viscosity allows for faster jetting and a thinner layer of ink. The result is more visually pleasing output due to the reduction in visible microstructure effects that you might see in thicker layers of UV ink,” adds Moffett.
An ink’s viscosity level also factors into the life of a printhead. “The low viscosity follows the requests of the new printheads that have drops with increasingly lower picoliters and for a lower impact on the printheads themselves. A low viscosity requires lower operating temperatures and a lower voltage so the printhead is less stressed and increases the life,” shares Ronchini.
Viscosity levels continue to decrease. “It’s doubtful that we’ve reached a point where ink chemistries are sufficient to jet at small enough volumes and high enough firing frequencies to support the printhead technology in development,” admits Edwards.
Indoor applications like wallpaper or wall decals placed in sensitive environments such as hospitals or educational settings require low-odor UV ink. “Low odor goes hand in hand with less potentially hazardous substrates in the air,” note Baumgartner and Eicher. It is because of certifications like GREENGUARD or GREENGUARD Gold that they believe lower odor levels can be achieved.
“Lower odor ink is necessary for certain applications like printed material that can quickly end up on retail shelves or in the hands of the consumers. This could potentially continue to be an area for improvement but that will be driven by demand,” admits Serafino.
Edwards agrees it is important that prints are chemically and environmentally inert to ensure the health and safety of print providers’ customers. In addition, “continuing advances in wide format print quality make it more likely that these inks will be used for consumer applications such as product decoration and décor; increasing the likelihood that they will be closely viewed or even handled by users, so we should expect the trend to lower odor inks to continue in concert with improvements in print quality.”
Vibrant Color
Another development involves color, specifically, more vibrant colors that resist fading as well as stronger looking blacks. Color is an essential component to a digitally printed piece, no matter the material printed to or where that final graphic is installed. The inks used here must live up the intended color communicated in the prepress stages of a job.
“Vibrant color that doesn’t fade is so important because color—and the way it attracts your attention—is a tremendous branding component. A strong looking black will make the bright constructing colors appear even more vibrant. Customers will not like to see their brand colors appear dull or faded, and the industry will continue to make improvements in order to achieve that high-quality standard that customers expect,” explains Moffett.
According to Edwards, all pigmented inks include ground particulates as colorants, meaning they are susceptible to UV light induced color fade. “Choosing pigment materials that more naturally resist fading, reducing pigment grind sizes so that more robust pigment-rich ink film thickness can be deposited, and building ink carrier chemistries that also more naturally resist UV light, can all help to improve color fade performance.”
For outdoor applications specifically, inks must be highly resistant to fading. As such, Baumgartner and Eicher believe there is a high demand on both the lightfastness and long-term stability of an ink. “Color fading is mostly dependent on the pigment chemistry. More stable pigments lead to better lightfastness.”
“Strong, vibrant colors in addition to dense, rich blacks that resist fading will always be important for development, whether it be for UV or UV LED ink. These vibrant colors will help create impactful, eye-catching prints that showcase near-photographic print quality no matter where they are displayed, indoors or out. These qualities remain important for ink development as manufacturers work to continually improve ink lines and formulations,” agrees Serafino.
Down the road, Northup believes that vibrant colors and richer blacks will not only be achieved to cater to traditional applications like signage, but also newer, up-and-coming digitally printed applications like packaging and manufacturing. “As the color gamut and durability of UV inkjet continues to improve, the range of applications will expand.”
Innovations in the Space
The newest ink introductions in the UV ink space focus on durability, flexibility, “green”-ness, and expanded color gamuts.
Canon UVgel ink technology in general, and particularly the most recent introduction of UVgel 460, changes some key behaviors of UV-curable inks. UVgel inks feature a natural, passive dot gain control mechanism built into their design. Rather than flowing freely over the media surface until they begin to dry or until they are exposed to UV energy, UVgel inks quickly gel in place on contact with the media before exposure to UV energy. This gelling action passively limits the dot gain for a precise, reliable, and repeatable dot size and shape on the media and ink film thickness.
Epson engineers continue to research innovative ways to improve ink chemistry technology. The SureColor V7000 flatbed introduces a new ink set—UltraChrome UV ink—that offers red and gray in addition to standard colors. White ink is included for use on wood, glass, and metal; varnish is an option for added texture, shine, or special effects.
Epta looks to produce the Swiss army knife of UV ink—one that is cured with old and new technology, and a hybrid ink that allows for printing on different types of materials, be they rigid or flexible.
Fujifilm recently introduced high-adhesion inks for some of its high-productivity flatbeds to better meet the needs of print providers. Uvijet HM UV LED curing ink is exclusively designed for the Acuity Prime Series of printers offering excellent dot reproduction, strong vibrant lightfast colors, and the versatility for printing both rigid and flexible sign and display applications.
Some of the latest developments from Marabu involve formulating UV inks that are thermoplastic polyolefin or TPO free. This is part of Marabu’s green commitment providing high-quality inks while balancing health and safety as well as the environment. Other innovations include inks with improved adhesion to a range of substrates such as glass or acrylic and more flexible inks for applications such as thermoforming and three-dimensional printing.
Mutoh’s new PJUVG5 ink for the Mutoh PerformanceJet 2508UF UV LED printer offers excellent adhesion to most substrates, a large color gamut, up to two year outdoor durability, and is stretchable up to 260 percent.
Roland recently announced ECO-UV 5 (EUV5) ink, which expands color gamut with the introduction of orange and red. The new options widen the EUV5 color gamut, enabling VersaUV LEC2-640 and LEC2-330 users to target previously unreachable colors. The EUV5 inks are designed to adhere to a range of coated and uncoated media, including foils, paper, clear film, and vinyl.
Neon colors like yellow and pink are also hot. With these two inks, swissQprint can produce four color variations—neon green, orange, pink, and yellow. The UV-curable, acrylic-based FS1 Neon inkjet ink series brings the glow of neon colors to inkjet printing. FS1 Neon is suitable for indoor applications and for a range of substrates used in sign making, offering high luminosity.
Considerations
Print providers should factor in current and future applications when choosing their UV ink, whether it’s a conventional configuration or UV LED. From there other considerations center on the printer itself, the green-ness of the ink, and adhesion levels, in addition to others.
The applications truly dictate what ink is used. Northup says questions need to be asked and answered like “are they going to be using the ink for applications that require flexibility such as car wraps or banners or primarily printing on rigid substrates such as aluminum composite material panels where adhesion is key?”
Furthermore, he explains that “point of purchase applications require large color gamuts and glossy finishes to meet branding requirements. Safety and exterior wayfinding signage need durability and chemical resistance. Due to the chemistry of UV ink, it may not be possible to get all of these properties in a single ink. For instance, to get better adhesion you might have to compromise on color gamut so you need to understand the top applications where the ink will be used.”
“It is important to consider the applications and potential clients a print provider is looking to serve; depending on the end use, it is important to consider every facet. For example, some clients require UL GREENGUARD certification, such as hospitals or schools,” agrees Serafino.
After that, it is of course essential that the ink work with your printer. “Stability and the easy and quick retrieval of the product makes the printer sleep soundly, of course, and if not secondary, a quality ink free of hazardous substances and that does not smell to create a more pleasant and healthy working environment. Another basic point is the written warranty of the manufacturer,” recommends Ronchini.
“Print providers should evaluate their key properties. While for one customer the adhesion on their key material may be the most important factor, resistance against chemicals or mechanical wear is much more important for another. The UV ink should cover most or all of these. Properties to consider are adhesion, blocking, flexibility, resistance, and health aspects. UV inks should contain as little hazardous substances as possible,” suggest Baumgartner and Eicher.
The functional performance of the ink is critical. “Ink performance will vary in terms of adhesion to the media, adhesion to other substances/inks, curing/drying performance, mechanical durability, chemical susceptibility, elongation, embrittlement, gloss uniformity, gloss variability, odor, and compatibility with coatings if desired. Some inks have remarkably poor performance in one or more of these areas,” cautions Edwards.
Continued Improvement
UV ink—whether traditional or LED—is popular for a number of reasons. As with anything, continued improvements mean a better product. Higher viscosities, wider color gamuts, and richer colors are all characteristics being tweaked and improved upon to offer print providers the utmost in quality when it comes to achieving exactly what their customers desire.
Dec2021, Digital Output