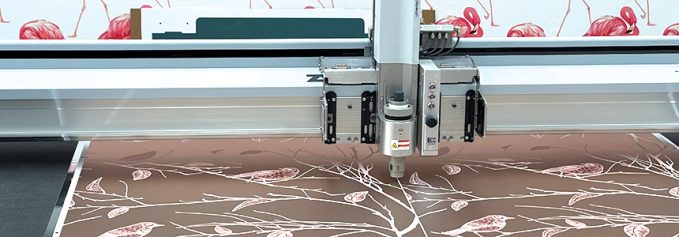
By Melissa Donovan
While many may consider the design and printing of a wallcovering to be more than half of the battle in achieving a quality graphic, the finishing aspect of the equation shouldn’t be neglected. If not cut properly, a beautifully designed and quality printed wallcovering can look unsightly. In addition, think of the wasted man hours in prepress and print production; the ruined media and ink; and finally, the unhappy customer if the deadline isn’t met on time. Automated finishing devices—from flatbed to roll, XY trimmers to laser cutters—can help achieve an end result worthy of praise.
Above: Wall Snobs of Fort Worth, TX cuts its digitally printed wallpaper with a Zünd cutting system.
Roll vs. Flatbed
While many service providers operate printers in house to produce wallcoverings or wall graphics, they may not be readily equipped in the finishing department. Cutting larger panels or even contour cutting smaller wall decals involve roll cutters, flatbed cutters, and XY trimmers—each offer many benefits.
Choosing the type of device is based on a few factors. “The recommended machine needs to be determined by considering the amount of cuts needed per day, what type of material, and space available in the work area,” advises Steve Sheetz, sign industry product manager, international sales, Safety Speed Manufacturing.
It’s important to note that wallcoverings aren’t just one type of material. Paper, vinyl, film, and fabric are all used and each influences the finishing device. “Digitally printed wallcoverings’ main peculiarity is that they can be composed of various substrates. Based on the material chosen—coated paper, film, vinyl, or fabric—a different finishing solution exists. Professionals in this sector perfectly grasp the difference and are able to recognize their appeal,” says Matteo Muto, sales and marketing assistant, Valiani srl.
Part of the reason why Randi Kerkaert, senior product specialist digital finishing, Summa nv, prefers flatbed cutters and XY trimmers is their ability to completely cut through a material. “While cutting wallpaper material you need to remember you are cutting through the complete media. On roll cutters you generally perforate the media to tear it off afterwards, which adds to the workload and does not necessarily create a nice clean edge, which is necessary for the application.”
XY trimmers provide a number of features ideal for finishing wallcoverings. “XY cutters offer many features for horizontal and vertical slitting while also compensating for skew. This type of cutting equipment can have general use crush-cut type blades or shear-cut type blades specifically beneficial in films. Wallpaper panel configurations on these platforms offer extra rollers for proper feedings and tension control,” explains Raum Divarco, GM, Cutworx USA.
These types of devices also offer options like rewinders, which Maureen Damato, dealer account manager and Keith Verkem, product manager, Colex Finishing Inc., say are ideal for creating a fully automated solution for all wallpaper applications. “This complete finishing package offers quick turnaround times allowing wallpaper to be delivered to your customer in a timely manner.”
“The best option for efficient and accurate panel cutting is to utilize an XY cutting system, as it can be set to an accuracy tolerance for either overlap or butt joint installation for flexible media, up to 40-mil gauge thickness in many instances,” agrees Timothy Saul, senior marketing specialist – LFS finishing solutions, Canon Solutions America.
David Stevens, industrial applications manager, Trotec Laser, Inc., argues that the roll versus flatbed debate depends on the application. “Both roll and flatbed cutters offer many benefits. If your primary application is cutting large or long panels, it may be more beneficial to invest in a roll cutter, whereas a flatbed cutter might be better suited for cutting wall decals in various sizes.”
“Contour cutting would best fall to flatbed cutters. Flatbed cutters typically have some form of optical registration to properly locate the print to the intended cut path of the die line. These XYZ cutting platforms also come with the largest variety of tooling best suited for each application,” explains Divarco.
According to Beatrice Drury, marketing manager, Zund America, Inc., in addition to a flatbed cutter offering a large variety of tooling, it also provides higher levels of preciseness. “Especially for cutting larger or no-bleed panels, the accuracy of the cutting machine is critical. Achieving the required level of accuracy for these demanding applications involves not only a perfectly accurate drive system and material advancing, but also highly precise setup and registration features generally available only on sophisticated flatbed systems.”
With regards to a wallcovering in general, Divarco points out that this particular application requires a well-thought out work area. “If the panels are oversized the flatbed cutter may need to advance the material forward to cut and the exit side will need to be supported. Wrinkles can occur if an exit rewind is not present, or an extended table is not available. Static on certain materials make it imperative that the advanced panel never touch the floor to collect dust. XY trimmers have the smallest footprint but also require extra thought as to the speed of which they can process and where the finished panels will be placed.”
Tooling Requirements
Common tooling requirements for cutting wallcovering material whether paper, vinyl, film, or fabric range from standard knives and blades to laser options. Speed, pressure, and thickness are notable considerations related to cutting.
For paper, vinyl, film, and even magnetic materials, Sheetz suggests a utility blade. For fabric-based wallcoverings, a cutting wheel or rotary blade specialized for textiles is used.
“Tooling varies by application and ranges from tangential and drag knife cutters to crusher blades. Some XY trimmers utilize crusher blades on the Y axis and a fixed blade in the X axis. We have found crusher blades deliver a clean quality cut when trimming a range of non-woven material,” admits Chase Pender, marketing manager, Supply55, Inc.
Other XY trimmers could consist of a right and a left slitter, with optional slitters available depending on how many images are printed side by side. A benefit in this scenario, according to Damato and Verkem, is that these slitters are self sharpening.
Muto says special tools may be required to achieve precise and burr-free cutting of wallcoverings. “An oscillating tool with a very thin blade knife moving up and down is helpful with a tool depth calibrated according to the material to be cut. More general, what is relevant in tools like these is the strokes per minute the tool makes.”
It’s important to recognize that specialty substrates need to have even more attention placed on them. “Wallcoverings sometimes involve shiny or reflective materials, which can be especially problematic for cutting. Not all registration systems can reliably handle reflective materials and cutting inaccuracies tend to be particularly noticeable in, for example, metallic applications,” admits Drury.
Laser Cut
Laser cutting is something to keep in mind when finishing wallcoverings—this includes both dedicated laser devices as well as flatbed cutters that are able to include a versatile laser option.
“Laser cutters or engravers work with so many materials—wood, acrylic, fabric, cork, or paper. Not only can laser systems cut these substrates, but they can also be engraved with incredibly intricate and detailed graphics,” explains Amy Dallman, marketing communications specialist, Epilog Laser.
Since laser processing is non contact and tool free, Stevens sees it as advantageous. “A laser has the advantage of no contact to avoid material deformation and keeps the material in place during the cutting process through downdraft suction, carefully securing the material without warping or stretching.”
However, not all material is ideal. For example, “anything natural can have a slight discoloration on the edges, paper-based materials especially. Also anything PVC-based should not be cut using a laser as this has some hazardous results,” advises Kerkaert.
While “laser cutting systems can offer a tremendous amount of versatility in terms of the many wallcovering materials they process, including paper, film, and fabric, lasers are not recommended for processing any vinyl materials that contain PVC or chloride, so it’s important to know the composition of your material before you invest in a cutting system,” agrees Stevens.
Fabric-based wallcoverings benefit greatly from laser options. “Fabrics have their own criteria for being processed and include factors such as being knit, woven, and if they are unsupported. Textiles need these factors considered for the final product to avoid unnecessary fraying or to achieve the best finish,” notes Divarco.
“The big advantages are mainly related to the low cost of the consumable compared to other technologies like knives and constant quality of cutting in a specific amount of time. This advantage becomes huge on some types of materials like fabrics that can be damaged from using a knife,” agrees Steven Leibin, president, Matik, Inc.
Overlapping Seams
When dealing with larger wallcovering projects that consist of multiple panels, overlapping must be addressed. In determining where to cut a wallcovering, it’s often important that material is left for overlapping or butting up seams correctly. Automated and semi-automated devices aid in achieving this goal successfully thanks to their powerful software solutions.
“The accuracy required for achieving industry standards—and better—is the result of a combination of machine accuracy—in cutting and material handling—and the precision in the steps leading up to the actual cutting, for example in the placement and capture of registration marks,” notes Drury.
Camera or optical recognition capabilities are helpful in this instance, as they are used to account for skew and/or distortion. “Certain sheer materials display significant differences of the seams and the cleanest cut determines how successful the panels visually meet. While heavier or less transparent materials are more forgiving, the cleanest end cut is the most visually appealing. These factors are key in complex wall designs that require many aspects of the design to seam flawlessly panel to panel,” explains Divarco.
Physical components of the actual cutter also aid in accurate overlapping and seaming. “Flatbed cutting plotters with wide cutting areas allow for trimming the material up to the edges. In addition, some solutions are equipped with a vacuum pump, which together with a fold-away button holds the material tightly onto the bed. Then the operator just needs to smooth the material up to the side of the trim and crease it into the corner,” shares Muto.
XY trimmers equipped with self-sharpening blades are key to providing accurate cutting, especially when butt joint wall installation is the focus, adds Damato and Verkem.
“When using a laser cutter, some software allows for preprogrammed processes that can contain repeatable and consistent designs that include the required overlap. Versus manual operation, the laser is simple to change designs/dimensions and has the benefit of accurate and precise cutting. In addition, small reference notches can be placed onto the graphic design edge, allowing the finished cut material to be lined up perfectly during installation,” says Stevens.
Moving Away from Manual
Some print providers might consider hand cutting wallcoverings. A semi-automated or fully automated device is beneficial versus a manual cutting apparatus because it can save in space, time, and costs.
Not surprisingly, an automated piece of equipment is much smaller than a table to hand cut. “Although hand cutting can be used as the finishing technique, one needs to consider the amount of footprint required in a shop. The size of the tables to cut ten-foot panels will take up space and consider the quantity of tables needed to keep up with production schedules. Either a flatbed or XY cutting system will have one footprint compared to the manual process that may need several tables to produce the work,” suggests Saul.
“Even though ‘handmade’ sounds charming, with many types of wallcoverings visual appeal is the primary objective, inaccuracies—e.g. from one panel to the next—are unacceptable. For manual processes to produce both accurate and repeatable results there is usually a great deal of setup involved and the potential for error and all associated costs in terms of time and money are considerable,” shares Drury.
While Sheetz says yes, hand cutting is always an option, the method is more time consuming and not as accurate as using a piece of hardware, “which allows the machine operator to quickly setup and execute cuts having the material fully supported on the machine frame rather than laying material on a table and cutting by hand.”
“Time is money, so if production volume and speed are important, then it will be more beneficial to invest in an automated cutting device rather than rely on hand cutting. Automated cutters such as laser systems can drastically increase your production volume, especially if the materials have intricate details that would be too time consuming to manually cut, and some laser systems even often integrated camera software to make perfect cuts around preprinted materials,” adds Stevens.
Dallman agrees that camera software is an huge advantage here. “Camera recognition capabilities aid immensely in ensuring cuts and marks happen exactly where they are supposed to.” For example, some systems feature multiple overhead cameras that allow the user to see a real-time image of a laser bed so operators can precisely position their artwork—whether it’s cutting or engraving—on their material in less time. An additional camera at the lens assembly can also be used for finding registration marks on preprinted pieces.
“While a short run might be less affected by inefficient processes, larger runs and projects on premium products are best left to automated cutting equipment. Human error variables can become expensive when reprints or lost material need to be accounted for. Manual options are only ideal when automated equipment is already in use or has a full schedule,” suggests Divarco.
Pender notes that in addition to automated systems offering improved accuracy over hand cutting and reduced labor costs, they also offer direct integration into the digital printing workflow. Many of these devices are supported by popular RIP platforms.
“This point is strictly connected with industry 4.0 production protocol, enabling the communication between all machines involved in the production process like printers and converting machines, in order to provide shorter time to market from order to delivery,” adds Leibin.
Being profitable means reducing costs. “As we all know a major cost in any production is labor. If you are manually cutting these items it will take a lot longer to align and cut them. Especially at such long lengths. Furthermore, a machine will be more accurate to align with the print,” explains Kerkaert.
“Machine cutting can finish at least ten times faster than hand cutting of graphics. Automation in machine cutting is designed to increase speed of setup, cutting, and final processing. A print provider should think about real estate, overhead, labor, and profit margin when comparing automation versus the manual process,” advises Saul.
Precision and Accuracy
Wallcovering production presents nuances on the finishing end that are addressed with automated and semi-automated cutting devices. The software that powers these cutters combined with the versatile tools—knives, blades, or lasers—is designed to address issues that affect wallcoverings like seams, overlapping, and working with large panels. A demanding application, wallcoverings require precision and accuracy from prepress to finishing and beyond.
To learn more about finishing for wallcoverings, visit digitaloutput.net/webinars and register to view an archived broadcast on the topic.
Jan2022, Digital Output